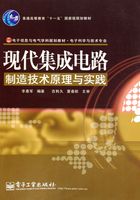
1.7 直拉法生长硅单晶
制造半导体器件及集成电路的硅基底材料要采用单晶体。在生产半导体器件及集成电路管芯的各个环节中,构造不同要求的器件结构区还需要制备特定规格的体单晶或单晶薄膜。因此,晶体生长[8]是半导体材料制备中极为重要的课题。
1.7.1 晶体生成技术的发展现状
晶体生长作为一个学科领域,已形成了近百年的研究历史。在这期间的主要研究成果包括:20世纪20年代,柯塞尔(Kossel)等人提出的完整晶体生长的微观理论模型,20世纪40年代,弗兰克(Frank)等人发展起来的晶体缺陷的诱发及生长理论,20世纪50年代后期,伯顿(Burton)等人在晶体生长及其界面的平衡结构领域取得的一系列研究成果,随后,杰克逊(Jackson)提出的平衡界面理论(使晶体生长从生长技术的研究进入微观理论模型的定性解释和定量的研究阶段)。
近年来,随着计算机技术的广泛应用,晶体生长理论的研究逐步向微观理论模型的定量计算方面大踏步地前进。
获得优质单晶体、生长单晶体的方法很多,在半导体材料的单晶体生长领域,伴随着半导体科学技术的迅猛发展,特别是硅单晶体材料的生长理论和技术发展很快,已趋于成熟。
热力学理论认为:材料结构形式的转变、晶体生长,是一个动态过程,是一个由非平衡态向平衡态过渡的过程。当某一晶体结构体系达到两相热力学平衡时,并不可能生成新相。只有在旧相处于过饱和(过冷)状态时,才会出现新相。当热力学条件处于亚稳区时,才有可能有新相生成,并不断使相的界面向旧相的方向推移,由此完成由成核到晶体长大的完整过程。
1.7.2 晶体生长技术的分类
晶体生长的方式可以分为3大类。
(1)固相生长方式
固相生长方式是通过固-固相转变完成的晶体生长过程。例如,石墨原体经高温、高压的强力条件下获得金刚石。又如,近年来,出现的“图形外延技术”,是在激光照射下完成的微晶硅向单晶硅薄膜转变的固-固相转变的过程。
(2)液相生长方式
液相生长方式包括溶液中生长和熔体中生长两种。溶液生长的发展历史已很久,能够获得的晶体种类很多。在半导体材料的制备中,GaAs 液相外延是最典型的溶液生长过程。以硅的单晶生长为例,获得硅体单晶的生长过程是从熔体中生长晶体的典型实例。
(3)气相生长方式
气相生长方式是由气相向固相晶体转变的气-固相转变的过程,属于气体凝华过程。半导体器件和集成电路管芯制造过程中所采用的化学气相淀积(CVD)方式即属于这种方式。
1.7.3 硅直拉单晶生长技术
下面以由熔体中生长单晶体的液相生长方式为例,介绍单晶硅的直拉生长技术。
从熔体中生长体单晶,是当前制备半导体单晶材料的主要方法。例如Ge、Si、GaAs、InP等单晶材料,都是从熔体中生长获得的。因为,这种生长晶体的方法具有生长过程在熔点附近性能稳定的特点,不易发生分解、升华和相变。
熔体生长是一个典型的液-固相转变的过程。在此相变过程中,生长的原子或分子要完成从无序的随机性排列转变为有序的排列,从无对称性转变为有对称性的阵列结构。同时,伴随着相的转变还要释放出相变潜热。这种相变不是一个整体效应,而是由固-液界面不断推进逐渐完成的一个类似正常凝固的过程。
在晶体生长过程中,为保证晶体生长顺利进行,必须考虑解决热量输运和质量输运的问题。通常,在气相和溶液中生长晶体时,质量输运起重要作用。在熔体中生长晶体,主要是热量的输运问题,它将直接影响晶体生长参数、生长界面的形态和晶体的完整性等。
图1-22所示为在直拉单晶炉中生长单晶体的热传递过程示意图。

图1-22 单晶生长过程中的热传递[9]示意图
如图1-22所示,直拉单晶生长过程中的热量传递包括以下几种方式。
● QH:加热器传到坩埚的热量。
● QRC:坩埚向外辐射的热(主要在坩埚的底部)。
● QL:熔体向固-液界面传导的热。
● QRL:熔体向外的散热。
● QF:相转变时放出的相变潜热。
● QRS:晶体表面的散热。
● Q'C:从固-液界面传走的热。
将晶体表面的散发热 QRS与固-液界面传走的热Q'C之和定义为QC。
在实际的熔体生长过程中,大部分氧以一氧化硅的形式逸出。SiO2凝聚在炉膛的内壁,影响了单晶炉的清洁度。使用这样的坩埚生长单晶将会含有大量间隙氧,这一点可能是有益的,也可能是有害的。这是因为,石英中可能含有足够多的受主杂质,将会限制生长出的单晶电阻率的上限值。因此,石英坩埚本身的纯度也影响硅单晶成品的纯度。熔体中碳的存在会使石英的溶解速度加快一倍。一种可能的反应如下:
C + SiO2→SiO + CO
大直径单晶炉的坩埚直径与其自身重量之比近似为1或比1稍大一点。通常,装料为12 kg、20 kg和30kg时,石英坩埚的直径分别为25 cm、30 cm和35cm。甚至已有人建议使用45 cm-65 kg的组合,所用石英坩埚的壁厚为0.25cm。在这种情况下,石英坩埚强度不够。因此,必须使用基座作为机械支撑。在冷却时,坩埚里的硅和石英之间的热膨胀系数失配常常会引起坩埚的破裂。
已经实现采用 CVD 法沉积获得的氮化硅作为坩埚材料。这种材料之所以具有吸引力,是因为这种方法曾用来从单晶中清除内含的氧。但是,氮化硅也会被侵蚀而引起晶体中的氮掺杂。氮是一种惰性元素,具有弱性施主的特征。CVD方式所获得的氮化物可以满足坩埚纯度对氮化物材料的要求。然而,这种方法尚处于实验阶段,还需要进一步完善。
石墨基座是用于支撑石英坩埚的,因为石墨的高温性能好,所以被选做基座材料。通常规定必须使用高纯度石墨,如核子纯度的石墨。为了防止在高温下晶体被从石墨中挥发出来的杂质所粘污,必须使用纯度极高的石墨。除基座外,处于单晶炉热区区域范围内的其他石墨部件也需要极高的纯度。基座被安装在轴架上,轴架的轴杆连到电动机上以实现转动。通常,整个机组应可以升降以保持熔体液面与固定参考点之间的相对距离不变,这是自动控制晶体直径所必需的。
作为炉子外壳的炉膛必须满足若干准则。它应该为处理炉子的内部部件提供方便,以利于维护和清洁处理。炉子的结构必须气密以防止大气污染,并且要有特殊的设计要求,不允许炉膛的任何部分变得太热,以至于炉膛中的蒸气压变化成为晶体粘污的因素。通常,单晶炉中的最热部分是水冷的。一般来说,加热器和炉壁之间是隔热的。
为了熔化硅材料,采用射频(高频感应加热)或电阻加热。高频感应加热用于小容量的熔体。但在,大单晶炉中只采用电阻加热方式。在目前所用的功率范围内(约数十千瓦),电阻加热器通常是较小、较便宜、更容易配备仪器和更有效的。石墨加热一般接直流电源。
1.7.4 硅直拉单晶设备
拉晶装置必须以最小的振动和很高的精度控制生长工艺的两个参数:提拉速度和晶体的转速。例如,制备的籽晶要有精确的方向性。籽晶杆和提拉机构必须保持精确的垂直于熔体液面。引导螺杆常被用于提拉和旋转单晶。这种方法容易使单晶对准坩埚的中心。但是,如果要生长很长的单晶就需要很高的设备。由于难以在整个拉杆内达到精密的机械误差范围,因而可能要采用钢绳提拉法。当使用钢绳时,使单晶和坩埚的中心对准比较困难。而且,钢绳提拉虽然平稳,但容易引起摆动。然而,由于钢绳可以绕到鼓轮上,机器高度就可以比类似的、使用引导螺杆的机器小。晶体通过净化管道离开炉子,在净化管道中,保护气体(如果有的话)沿着晶体表面流动以冷却晶体。晶体从净化管道进入上炉膛,通常上炉膛由一隔离阀与炉子隔开。
硅的单晶生长法必须在惰性气体或真空中进行,即气氛控制。这是因为热的石墨部件必须进行保护,以防止氧的侵蚀,工艺中所用的气体应该不与熔融的硅起反应。只在真空中生长单晶方能够满足这些要求。还有,可以从系统中除掉一氧化硅,从而防止一氧化硅在炉膛内部的沉积。
集成电路的高集成度和高可靠性要求使得它对工艺衬底片的质量有着极高的要求,而集成电路制造对硅单晶体的晶体取向和掺杂浓度的精度也有极高的要求。当集成电路的集成度达到超大规模的层次时,电路中的元器件电性区域已在微米数量级的水平上,电极布线尺寸以及电极间的线间距更是处于亚微米的层次,这样,硅工艺衬底片体内的晶体缺陷或缺陷群,以及在每道高温工序环节引发的诱生缺陷,都会造成局部的杂质梯度的异常分布,从而造成电性区的局部甚至是整体失效,以及 PN结结面不平整而引发单结特性变差。所以,随着集成电路的规模继续扩大,对工艺衬底片的结晶质量要求也会更高。
图1-23所示为直拉单晶生产设备装置的结构示意图。图1-24是直拉单晶生产设备及生产现场的照片。

图1-23 直拉单晶生产设备装置结构

图1-24 直拉单晶的生产设备及现场
生长单晶硅的过程是非常严格的。主要表现在对原材料的纯度和洁净程度要求极高。在单晶生长的工艺过程中,工艺条件的控制精度要求也极高。否则,制备出的半导体材料往往是不符合质量要求的,一是材料的纯度不够,二是晶体的结晶质量不符合要求。制备出合格的单晶硅之后,还要经过定向切割、表面研磨和抛光(通常有化学抛光、机械抛光及化学机械抛光三种抛光方式)。
1.7.5 硅直拉单晶工艺步骤
直拉生长硅单晶的基本步骤如图1-25所示。

图1-25 直拉单晶生长工艺步骤示意图
拉制出完美的单晶,首先须精心“选种”、“育种”,并认真做好“下种”前的准备工作。从晶体开始生长到晶体长大,都必须创造出一个良好的晶体生长环境——稳定的温度分布场,并认真控制好固液界面形状。
拉晶前对所用的原料、原材料和设备等,均须经过严格的检验和清洁处理[10]。例如,选用无氧化夹层、纯度符合要求的多晶硅料,使用无气泡、无白点的石英坩埚,特别要做好对籽晶的选择、加工和处理工作。籽晶也被称为晶种,是引导单晶生长的种子。籽晶的质量直接关系到随后单晶体的成核及长大,籽晶的质量对日后制备成的晶体的完整性和电阻率分布也有一定影响。籽晶通常根据产品规格的要求选用与拉制单晶同导电类型、同晶体取向、电阻率较高的无位错单晶来制备。
籽晶的直径原则上在能承受晶体重量的基础上,截面尽可能小些,这样有利于抑制晶体的位错。特别是要求熔硅的预接触面要求无微细损伤、平整、光洁,截面通常切成正方形形状,为此,籽晶必须通过精确地晶体定向、切割、研磨、腐蚀、抛光、清洗和干燥等加工处理。
装炉前必须对单晶炉膛和单晶炉内的各个部件进行极为严格的清洁处理,以防止拉制单晶过程引进粘污或掉渣。随后,便是装料和安装籽晶。多晶硅料须装成“山”字形,装正,且勿接触坩埚边。熔硅前,预先打开炉体各部位的冷却水,接着抽真空或通氩气。升温之后要严格控制固熔硅的时间、化硅速度、坩埚的转速等,使硅料从锅底开始均匀、缓慢地熔化。当出现有“熔偏”、“挂边”、“架桥”、“硅跳”等不正常趋势时,须适当调整输入功率、坩埚位置等使其恢复到正常的熔硅状态。
整个直拉硅单晶的过程包括:引晶(下种)、缩颈(细颈)、放肩、等颈生长和收尾等诸工艺阶段,如图1-25所示,以下分别予以简要叙述。
① 引晶(下种)
当多晶硅料全部熔化后,调整引晶功率和坩埚位置,使熔硅的表面温度稍高于硅的熔点。调整籽晶转速并降至距离液面3~5mm的位置处预热(或称为烤晶)几分钟,以利于单一晶核沿籽晶成核长大,避免寄生晶核的诱发和生长。预热一段时间之后,下降籽晶至熔硅表面让其充分熔接,此时需注意控制引晶的温度。温度过高,会使籽晶熔断;温度过低,易产生多晶。生产中常通过调节功率和坩埚的位置,以及观察液面波动、液面颜色等多种方法来寻找最佳引晶点。熔接后,通常根据籽晶界面的光圈、棱点、固液界面形状和直径比较等方法来判断熔体温度,以控制单晶的正常生长。其中,尤以“界面光圈法”最为有效。所谓“界面光圈法”是指在熔接后界面处会逐渐产生光圈并逐渐变圆,此时的引晶温度最合适。如果引晶后籽晶周围不出现光圈,甚至产生一圈结晶,表明熔体温度过低,反之,熔接后立刻出现抖动的光圈,则说明温度太高。
② 缩颈
通常,采用“高温熔接、低温快速细长缩颈”技术对生长无位错单晶是一种行之有效的方法。当籽晶和熔硅浸润良好,在界面很快形成结晶胚芽时,适当地降低温度并缓慢提拉籽晶,通过对温度与拉速的协同调节,便能长出规定尺寸的细颈来。此刻,可以观察到在<111>晶体取向生长的细颈表面出现3条均匀分布的棱线,即“晶棱”。晶棱随细颈缩小转为宽平,并可见有反光或在细颈某一侧面向外鼓起,这都是无位错单晶正常生长的标志。
③ 放肩
放肩阶段是指从缩径到要求长度后将晶体放大到所需直径这一段时间的操作过程。通常采用大幅度地降低提拉速度通过观察光圆形状、棱面变化或界面亮度等方法,控制出一个均匀平滑的晶肩。近年来,推广“大角度平放肩”工艺,这种工艺不仅提高了单晶的利用率,缩短了放肩时间,而且能成功地拉制出无位错单晶。
④ 等径生长
放肩至接近所需直径时,适当升温,增加提拉速度,使晶体圆滑地转入等直径生长阶段。等径生长通常采取恒定拉速以使直径大小均匀。
⑤ 收尾
等径生长之后,往往拉成一个锥形尾体,目的在于减少尾部位错的产生与攀移。
在以上叙述的拉晶过程中,特别是在高真空下拉制高阻单晶硅时,杂质的挥发和粘污影响随时间的增长而加大,从而影响单晶的电阻率值和电阻率的均匀分布。为此,必须严格控制熔硅、缩颈、放肩等过程的速度、时间和温度等工艺参数。
图1-26和图1-27所示为现代化的硅单晶晶圆片的研磨设备。图1-28和图1-29所示为硅单晶生长过程中放肩及等颈生长时所拍摄的实景照片。

图1-26 硅单晶研磨设备1

图1-27 硅单晶研磨设备2

图1-28 硅单晶生长——放肩结束

图1-29 硅单晶生长——等颈生长