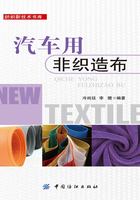
第二节 纤维特性对汽车用纺织品性能的影响
纤维是组成纱线的基本要素,纱线是织物的主体,采用什么样的织物组织结构,是根据汽车设计师的具体要求而定。为了满足汽车设计师对某一车型汽车结构和内装饰用纺织材料的设计要求,供应商与纺织工程师,首先要确定织物的组织结构,然后确定纺纱工艺系统、织造与后处理工艺方案,当这一系列工艺技术方案确定后,如何完成实施工艺方案,最重要的因素还取决于纤维原料的选配。纤维原料的特性是达到最终产品技术要求的基础,纤维的力学性能直接影响着最终产品的应用性能,所以,必须研究纤维的特性与汽车结构和内装饰纺织材料性能之间的关系,以便充分发挥纤维特性,开发出应用性能最理想的汽车用纺织材料。反映纤维特性的指标很多,只选择一些重要的常用的参数加以介绍。
一、长度
天然纤维的长度具有很大的差异性。相对来说,羊毛纤维平均长度较大,一般在50~100mm之间;而麻纤维的主体长度只有25~36mm;亚麻纤维的平均长度更短,只有17~20mm。当使用这些纤维加工不同组织结构的织物时,在成纱过程中,无论采用什么样的纺纱工艺系统,纤维在纱线中的特性的体现是有很大区别的。纤维越长,在成纱过程中,纤维与纤维之间的抱合力就越大,因为纤维之间的抱合力是靠自身在成纱过程中相互间的摩擦所形成的,纤维越长,相互接触的面积越大,摩擦产生的抱合力越大,所以成纱后的纱线强力也就越大,形成织物后的机械强度也就越高,应用性能就越好。
同理,在利用纤维以非织造布生产工艺加工新型汽车用纺织材料时,纤维网状结构的非织造布是依靠纤维自身缠结成网,针刺法、水刺法或缝编法非织造布,采用的机械钢针、高压水针或缝编织针都是将纤维网自身的一部分作相位移动,从而在纤维网中形成缠结链条作用,达到固结纤维网的最终目的。由此可知,纤维越长,形成的缠结链条就越坚固,形成的非织造布强度就越大,延伸弹性就越好,刚性就越强,所以在汽车内饰中的应用性能就越理想。曾有试验表明,同样平方米质量的条件下,由于纤维长度的不同,较长纤维的纤维网,其强力大于较短纤维的纤维网。同样工艺形成的非织造布,纤维长度增加10%,其最终产品的机械强度将提高15%~30%。若纤维长度降低20%~30%,最终产品的机械强度将下降40%~50%。掌握这一规律之后,一旦确定了某种汽车用纺织材料的成纱线密度或非织造布的纤网定量后,若想使最终产品机械强度达到最大化,必须选用较长的同种纤维,以实现工艺方案的最终目的。
当然,纤维长度的选择,一方面要考虑最终产品的应用性能,同时还要考虑生产加工过程中的工艺系统。通常较长纤维要选用精梳、半精梳毛纺纺纱工艺系统或化学纤维中长纺纺纱工艺系统,而较短纤维,如棉纤维、亚麻纤维则需选用棉纺纺纱工艺系统,这样,使纤维在开松梳理过程中损伤较小,同时,又能充分发挥纤维长度特性在成纱和织物中的作用。为此,化学纤维在长丝切断成短纤维时,按其长度范围不同,又分为棉型化学短纤维32~38mm、毛型化学短纤维50~110mm、麻型化学短纤维38~54mm、非织造布或产业用型化学短纤维54~105mm、静电植绒超短纤维1~2mm。
在汽车用纺织材料中,吸音降噪,隔音减震材料,绝大部分用废旧再生纤维,主体长度更短,一般只有14~25mm。还有亚麻的落麻纤维,长度也都比较短,可它们正是替代化学纤维,降低制造成本的重要原料。毛混纺产品的废旧再生纤维,还有苎麻的精梳落麻,都被大量应用于汽车用纺织材料,这些废旧再生纤维长短差异很大,所以在加工新型汽车用非织造布的过程中,也要选用不同的非织造布生产工艺,尤其是纤维的成网方式,是截然不同的。通常较长的纤维一般采用机械成网方式,既有效地利用了纤维长度特性,又确保了成网的均匀性,还能达到汽车用纺织材料技术性能要求。较短的纤维一般采用气流成网的方法加工成纤网,然后再以不同工艺将纤维网固结,制成汽车工业用的各种非织造布产品。
那么,化学纤维长丝是无限长的、连续的,是由各种高聚物经过高温熔融挤压抽丝或溶液法湿法纺丝而成化纤长丝或直接成布,所以其产品的强力要远大于短纤维同类产品,由此可见,纤维长度对汽车用纺织材料的性能影响是至关重要的。纤维长度不仅影响加工制造成本,而且决定产品的风格,还关系到最终产品的应用性能,影响产品的使用寿命,几种常用纤维长度见表2-2。
表2-2 几种常用纤维长度范围

二、线密度
线密度是用来反映纤维粗细的物理指标,就纤维的线密度而言,天然纤维之间也有很大的差异。羊毛纤维的线密度范围为2.7~5.5dtex,亚麻纤维的线密度范围为0.01~0.10dtex;而棉纤维相对较细,线密度范围为1.0~2.0dtex,化学纤维线密度范围更大,最细纤维可以纺成0.001~0.010dtex,被称作超细纤维。无论是用纤维进行纺纱加工汽车内装饰材料,还是以纤维为原料,采用非织造布生产工艺,加工各种汽车用纺织材料,纤维的线密度都是一个十分重要的技术参数。用于纺纱,纤维的线密度决定同一纱支中的纤维根数。
一般来说,纱线中的纤维根数与纤维的线密度成反比,纱线支数一定时,纤维越细,纱条中的纤维根数越多。纱线强度除受纤维长度及工艺条件影响外,直接取决于纤维的细度。纤维成纱是靠纤维之间的抱合力,而抱合力依靠纤维间的接触点和接触面积;纤维长度一定的条件下,纤维间接触点的多少和接触面积的大小,完全取决于纤维的细度。接触点越多,接触面积越大,纤维相互之间的滑移可能性越小,也就是说相互产生的抱合力也就越大,因此,成纱后单纱强力就越大,反映到汽车用纺织材料的织物上,力学强度也就越大,应用性能就越好。
在以非织造布生产工艺加工汽车用纺织材料的过程中,同样是纤维越细,单位定量纤维网中,纤维的根数越多,纤维网的强度越大。曾有试验表明,纤维线密度减少1.0dtex,对同平方米质量纤维网的强度可提高8%~12%;如果纤维线密度增加1.0dtex,对同平方米质量轻薄纤维网的强度可降低15%~25%。当然并不是说纤维越细越好,过细纤维无论纺纱还是加工非织造布,都增加了混合、开松、梳理的难度,纤维越细,一般说来,强力就越低,所以在梳理过程中,分梳成顺直平行的单根纤维状态,难易程度会更大,容易在梳理过程中形成大量毛粒,从而影响成网、成条、成纱的均匀性,反而影响最终材料的应用性能。
纤维似弹簧,纤维越细,自身弹力就会下降,当以细纤维加工弹性汽车用纺织材料时,产品的弹性变差。所以,一定要根据汽车设计师的具体要求,按照不同材料的应用性能和特点,选用不同细度的纤维原料。例如,以针刺法工艺加工针刺汽车地毯,地毯要求有良好的弹性回复率,所以,纤维线密度就应选择略粗一些,一般选择8~17dtex。如果毯面平方米质量较小,为增加覆盖率,使毯面质地紧密,混料中要适当混入少量的6~8dtex的纤维,有时为了增加地毯的弹性,还要适量加入16~20dtex粗纤维。由此可见,纤维的线密度对各种汽车用纺织材料的应用性能有着直接的影响,一方面影响加工难度;另一方面影响产品的加工成本,同时还决定最终产品的应用效果。几种常用纤维线密度范围见表2-3。
表2-3 几种常用纤维线密度范围

三、截面形状
纤维的截面形状也是用来反映纤维特性的一个重要技术指标。截面形状的变化,使纤维的特性随之发生了很大的变化,尤其各种新型差别化纤维。化学纤维截面的变化,主要是通过控制纺丝工艺,改进纺丝设备来实现,赋予化学纤维特定的功能性,以满足汽车工业及其他特殊用途的需求。天然纤维的截面形状是自然形成的,不同的纤维具有不同的截面形状。例如汽车坐垫和靠背芯需要纤维刚性强、弹性大、弹性回复率高、吸湿好,普通涤纶不具有这些特性,所以在加工涤纶过程中,改变其横截面形状,使其具有异形多孔中空截面形状,从而使改性涤纶,满足汽车内装饰材料的生产加工需要。纤维自身特性由横截面形状所决定,形成纱线后,纵截面形状也直接影响最终产品的应用性能,下面简单加以介绍。
1.纤维的横截面形状 天然纤维的横截面形状,是生长过程中自然形成的,差异不是很大。一般棉纤维的横截面呈豆状形、马蹄形、芯有瘪中空;毛纤维的横截面呈对称的鸭蛋形;各种麻纤维横截面基本都呈不等边的五角中空形。化学纤维除具有棉毛丝麻横截面形状外,已从单层向双层、向多层立体化方向发展。异形纤维的典型横截面有异形中空、多中空、混纤异形;复合化学纤维横截面形状多用镶嵌形、木纹形、多环形、放射线形、海岛形等;特殊用途化学纤维横截面形状,还可以加工成偏心形、对称形、棋盘形、梅花形等,如图2-2所示。

图2-2 各种不同横截面形状示意图
纤维横截面形状的不同,不仅决定了自身的特性,如刚性、弹性、强力、吸湿性、反光性、伸长率等,同时,还影响整个加工过程,直接影响最终产品的应用性能。天然纤维多以圆形、中空、扁平状横截面居多,它是自然形成的横截面形状。化学纤维横截面形状,开始也是按照天然纤维横截面形状仿制出来的,逐渐演变成满足多功能需要的各种各样的化学纤维横截面,如三角形、三叶形、中空管状形、扁圆形、扁带形、四角星形、五角星形,更复杂的有六角星形和八角星形等。由于纤维横截面形状的差异,同样线密度的纤维,其表面积大小就相差很多,纤维的表面积是影响纤维之间相互摩擦产生抱合力的关键,表面积越大,纤维之间摩擦机会越多,产生的抱合力越大,形成纤网、纱线或织物的力学强度越高,应用性能越好。有试验研究表明,星形截面形状的涤纶,比普通棉毛型截面形状的涤纶表面积可增加50%左右。
纤维横截面形状的变化,直接反映出纤维自身的刚性变化。有试验研究表明,如果与圆形截面形状的纤维硬挺度相比较,具有同样强度的三角形截面的同种纤维的硬挺度可提高20%;若采用椭圆形横截面的同样强度的同一种纤维,其纤维的硬挺度只有圆形截面纤维的一半。纤维截面形状的变化,对纤维吸湿性影响更加明显,异形多中空涤纶的吸湿性,比普通棉毛型截面形状的涤纶提高了80%~150%,从而满足了汽车内装饰材料舒适性的要求。
为了增加最终产品的回弹性、蓬松度、反射效应和吸音效果,在化学纤维的生产加工过程中,可以人为控制纤维横截面形状变化来得以实现。任何一种化学纤维新材料,绝大部分都是通过纤维横截面形状的变化创新来达到的。对化学纤维截面形状变化的研究,也是化学纤维工业的一种高科技,它会给纤维特性带来难以想象的功能性效果。
2.纱线的纵向形状 纱线的纵向形状也有很多变化,如不对称形、螺旋形、折叠形、串珠形等。天然纤维根据不同的种类和生长条件的差异变化也很大。用不同形状的纱线织造的织物所反映出来的织物外观也不同,有的织物风格朴素,有的自然大方,有的庄重、有的豪华,这些在汽车内装饰材料中得到普遍应用。
化学纤维刚刚问世时,由于生产工艺技术水平的原因,纱线的表面以光、亮、滑突出,使人们一下子很难接受这种极大的反差,无论手感、外观,还是悬垂性、吸湿性等,都不随人意。尤其应用于汽车内装饰材料,虽然满足了耐磨性和耐光性的技术要求,可其纱线的纵向形状的圆直效果,极大地限制了化学纤维纱线的具体应用,在汽车工业发展的初期阶段,汽车内装饰材料仍然是天然纤维织物占统治地位。
随着化学纤维工业的快速发展,当汽车工业发展进入成熟期时代,化学纤维纱线的纵向形状也发生了很多变化。应用先进的化学纤维生产工艺技术和化学纤维纺纱工艺技术,采用空气变形丝工艺,纺成化纤膨体纱、假捻变型丝化纤纱、实捻化纤纱、交捻化纤纱、起毛起绒化纤纱、异旦异染异色混纺化纤纱、交络混纺化纤纱、三叶中空疙瘩形化纤纱、单包复化纤纱、双包复化纤纱,还有圈包复化纤纱等。
通过化纤纱纵向形状的变化,使化学纤维纱线的纱线手感与花式远远超过天然纤维的传统产品,化学纤维纱线纵向形状的超天然化,极大地促进了化纤纱织物在汽车内装饰材料中的应用,使化纤纱由人们原来的不愿意接受,发展到后来,人们普遍认可,而且一改天然纤维织物统治汽车内装饰材料市场的格局,同时,还弥补了天然纤维色泽、光泽、外观风格、使用寿命、机械强度等方面的不足,使汽车内装饰材料的产品档次也有了很大提高。
由此可见,无论纤维的横截面形状变化,还是纱线的纵向形状变化,都直接关系织物的性能,也就是说,都决定着汽车用纺织材料的应用性能,影响着汽车内装饰材料的发展,几种常用纤维的纵横向形态特征见表2-4。
表2-4 几种常用纤维的纵横向形态特征

四、卷曲度
卷曲度也是用来反映纤维表面特性的一个非常重要的技术指标,卷曲是纤维沿轴向形成的弯曲现象,通常把单位长度内的卷曲数定义为卷曲度。弯曲的大小,即弯曲弧的半径被定义为卷曲曲率半径。纤维卷曲度和曲率半径整体形象地反映出一种纤维的弯曲特性、弹性好坏、刚性大小、延伸性能等。这种特性不仅决定了一种纤维生产加工的难易程度,也决定了在成网、成纱中所起到的具体作用,直接影响最终汽车用纺织材料产品的应用性能。
天然纤维的卷曲度是自然形成的,所以也称天然转曲。单位长度内的卷曲数和曲率半径变化不是很大,天然转曲数越多的棉纤维,一般说来,其品质就越好;天然转曲数越多的羊毛纤维的弹性、手感都要好于卷曲度低的纤维;曲率半径越大的羊毛纤维加工成织物后,产品的丰满度越高,弹性越好,手感也越柔软,高档感越强。纤维的卷曲度和曲率半径决定纤维相互接触时的状态,无论是纺纱织布,还是成网加工非织造布汽车内装饰材料,卷曲度高,曲率半径大的纤维,相互之间滑移摩擦阻力增大,相互摩擦抱合力较大,所以成网、成纱强度增加,然而在开松、梳理过程中难度增大,纤维损伤度增加,被机械拉断的机会增多,影响纤维成网的均匀性,当然无卷曲的光棒纤维的成网性更差。
通常用每厘米长度纤维天然或机械加工的转曲数来表示卷曲度,单位为个/厘米;也有用每英寸长度纤维所具有的卷曲个数表示。单位为个/英寸;还有用25mm长度纤维的卷曲数表示,单位为个/25mm。常用天然纤维和化学纤维的卷曲度为4~12个/cm,高卷曲化学纤维卷曲度每厘米最高可达几十个到几百个,这完全取决于最终产品的机械性能要求。
化学纤维的卷曲度是按照工艺要求人为控制的,可利用化学纤维内部结构的不对称性,而在热空气或热水中进行处理而形成纤维卷曲;也可利用化学纤维的热收缩性能,采用机械加压、高温定型或超声波的方法,使纤维单位长度内形成一定数量的锯齿形、螺旋形或其他形状的卷曲,以达到最终产品设计风格的要求。合理的卷曲度和曲率半径,不仅加工生产难度小,成网、成纱强度增加,还会大大改善最终产品的应用性能。例如采用毛涤混纺加工起绒类汽车内装饰材料,由于毛纤维的卷曲度高达7~14个/cm,纤维的曲率半径大,所以混纺涤纶必须选用卷曲度和曲率半径与毛纤维相近的,即选毛型涤纶短纤维,这样在加工过程中,工艺参数便于控制,成网、成纱、织布质量有所保证,起绒后产品的质地丰满,手感柔软,触摸温暖感强,有高档内装饰材料的风格,能体现出高档轿车的豪华尊贵感。
另外,在利用涤纶短纤维加工座椅垫和靠背芯产品时,为了确保最终产品的良好弹性和回复率,除采用高旦、高弹、多孔中空异型截面外,还要采用垂直铺网技术,纤维的卷曲度和曲率半径都要经过特殊设计,使纤维真正起到一种“假”弹簧的作用。由此可见,纤维的卷曲度和曲率半径,不仅决定其自身的特性,也决定着生产加工中的难易程度,更重要的是直接影响成网成纱的质量,也影响着最终应用性能,表2-5给出了几种常用纤维的卷曲数。
表2-5 几种常见纤维的卷曲数

五、表面性能
用来反映纤维表面性能的重要指标是摩擦系数,所谓摩擦系数是指纤维相互接触时,相对滑移的难易程度,难易程度越大,我们称其为摩擦系数大;纤维之间相互易于滑移,我们称其摩擦系数较小。如羊毛纤维表面呈鱼鳞片状,鱼鳞片状的高低、角度的大小,决定此种羊毛纤维的表面摩擦系数大小,摩擦系数越大,成网、成纱过程中,纤维之间的摩擦抱合力越大,成网、成纱、成布强力越大,最终制成的内装饰材料的力学强度就越高,应用性能就越好。如玻璃纤维表面呈圆滑的光棒状态,所以,在用于加工汽车顶棚内衬板和门内衬板时,成网强力低,为了弥补这一不足,利用其刚性大、变形小的特点,必须加入适量的丙纶短纤维,经过针刺模压热定型后,固结成一体玻璃纤维网,增强整体组件的力学强度。
随着科学技术的不断进步,纤维表面改性处理方法很多,比较典型的低温等离子体纤维表面改性处理技术已得到广泛应用。纤维的表面摩擦系数大,纤维间相互滑移时就增加了切向阻力,成网、成纱时纤维间的抱合力增大;但并非是纤维表面摩擦系数越大越好,纤维的表面摩擦系数也直接影响成网的均匀性,摩擦系数越大,纤维在梳理过程中,产生的静电越大,静电电荷积聚现象越严重,这势必影响纤维成网的均匀性;另外,纤维摩擦系数大,在开松梳理过程中,工艺难度增大,纤维损伤增大。在针刺法非织造布加工过程中,针刺阻力增大,钢针磨损严重,易造成断针现象,另外能耗增加,因此,必须在汽车用纺织材料生产加工过程中,根据产品的技术性能要求,要切实考虑纤维表面性能对最终产品的应用性能的影响因素,以确保生产工艺达到最终目的要求。几种常用纤维的摩擦系数见表2-6。
表2-6 几种常用纤维的摩擦系数

六、强度和伸长率
纤维强度和伸长率是直接反映一种纤维在受外力作用时所能承受的最大能力,强度越大,说明纤维品质越好,利用率越高,应用性能越好。棉纤维的成熟度越差,单纤维强度就越低;毛纤维的强度越大,说明可纺性越好,其织物的力学强度就越大,应用性能就会越强,用途就会越广泛。单纤维强度大,在开松梳理等一系列加工过程中,纤维的损伤就小,成网、成纱、成布的强度就高,品质就有保障。伸长率的大小,反映了纤维受外力作用时的延伸性状况,天然纤维的伸长率一般差异很小,而化学纤维由于生产工艺的不同,品种的不同,伸长率差异很大。纤维的伸长率大小,直接影响着成网、成纱、成布的产品伸长率和弹性,纤维的伸长率对汽车内装饰材料的模压成型组件来说至关重要,模压组件形变较大时,必须选用伸长率较大的同类纤维,否则,在模压成型过程中,由于纤维自身伸长率限制,将导致模压组件中的单层断裂,影响表面外观风格。伸长率选择不合理,也可能直接影响内装饰材料的规定厚度及均匀一致性。
无论是天然纤维,还是化学纤维,纤维的伸长率在干态状况下,不如湿态状况下的大。一般来说,湿态伸长率比干态伸长率可提高1.0~1.5倍,而强度则不然,一般来说,纤维的干态强度大于湿态强度,只有棉、麻纤维的强度随着纤维吸湿量的增加而增大,这是由于纤维素纤维内部结构所决定的。几种常用纤维的干湿态强度和伸长率变化见表2-7。
表2-7 几种常用纤维干、湿态强度和伸长率变化

七、吸湿性
纤维的吸湿性反映纤维在不同相对湿度状况下,吸湿能力的程度,这一特性也直接影响材料的力学应用性能,决定着产品的舒适性和使用寿命。从纤维的强度和伸长率特性可知,纤维吸湿后,伸长率普遍增大,这就使其在汽车用纺织材料应用中有规律可循。当使用棉麻纤维加工内装饰材料时,由于棉麻纤维随吸湿量增加,其纤维强度增大,所以生产工艺条件相对湿度要偏大掌控,充分利用棉麻纤维这一特性,既有利于纤维网的生产加工,又有利于成网、成纱、成布的质量的提高。
纤维吸湿性的大小,也是确定其生产工艺参数的基本依据。按照汽车设计师的要求,一种汽车内装饰材料的模压组件,不仅有厚度规定,更重要的是单位面积的质量限定,总体质量要符合设计要求,为了准确控制质量范围,必须掌握各种纤维原料的吸湿性。一般纤维的吸湿性能多用纤维的回潮率表示,各种常用纤维在不同相对湿度的条件下,吸湿性变化见表2-8。
表2-8 几种常用纤维在不同相对湿度条件下的吸湿性变化

【五级】❶温度为20℃。
纤维的吸湿性,是采购纤维原料公平性的重要依据,这是控制内装饰材料生产成本的第一关。在汽车内装饰材料生产加工过程中,每一道工序工艺参数的确定,都要考虑纤维吸湿性的因素,否则,产品质量就会受到吸湿性波动的影响,增加生产工艺难度。能否确保汽车内装饰材料的最终设计风格,纤维的吸湿性也起到了非常重要的作用。座椅面料如果选用吸湿性差的纤维,人们长时间在座椅上就会感觉不舒服,特别是在高温地区的夏季里,人们排汗量大,纤维本身的吸湿能力显得非常重要。即使是作为超真皮的基布材料,选用纤维也必须考虑其吸湿能力,否则超真皮透气性就相对下降,反映不出超真皮座椅的高档舒适感,因此说,纤维的吸湿能力与汽车内装饰材料的性能息息相关。
八、电学性能
纤维的电学性能是一种非常重要的技术指标,它反映一种纤维自身的特性,同时也决定着其使用量及应用范围。尤其对于汽车内装饰材料而言,纤维的电学性能对汽车内装饰材料功能性的影响更直接,反映得更明显。通常用纤维的介电系数、电阻和静电电荷等来反映某种纤维的电学性能。纤维是一种电绝缘材料,无论加工机织物或针织物汽车内装饰材料,还是生产新型非织造布汽车内装饰材料,都需要进行纤维混合梳理,靠纤维之间的摩擦抱合形成纤网和纱条,由于纤维介电性的存在,使其具有一定的质量比电阻,质量比电阻一般会随着纤维的吸湿而发生变化。在一般大气条件下,涤纶的质量比电阻可高达1013Ω·g/cm2,因此,在材料生产加工过程中,由于纤维之间、纤维与机件间的密切接触和相互摩擦,就会形成静电电荷,由于静电电荷在纤维和物体之间的相互转移,就产生了静电现象。带不同静电电荷的纤维与机件之间发生吸引,带相同静电电荷的纤维之间相互排斥,结果严重影响纤网形成的均匀性,最终影响内装饰材料的成品质量。
1.介电系数 理论实践证明,真空的介电系数等于1,空气的介电系数为0.75~1.0,水的介电系数为40~80,而干燥状态下的纤维材料介电系数一般为2~5。由此可见,水的介电系数比干燥状态下的纤维材料的介电系数大几十倍,所以纤维会随着回潮率或含水量的增大,介电系数增大。纤维材料的介电系数比空气介电系数大几倍,纤维在不同的环境条件下,其介电系数的大小也不相同,通常纤维的介电系数随着周围环境温度的升高而增大;随着噪声频率的增高,纤维的介电系数会减小。由于纤维材料的各向异性,纤维处于电场的平行或垂直方向,也会影响纤维的介电系数;纤维中含杂质的多少,也会引起纤维介电系数的变化。表2-9给出了汽车的内装饰材料生产加工中,几种常用纤维在不同条件下的介电系数。
表2-9 几种常用纤维在不同条件下的介电系数


2.质量比电阻 电阻是表示物体对电流起阻碍作用的物理量,也是反映纤维导电性能的物理量,它能直接反映某种纤维的电学性能,其单位是欧姆·厘米(Ω·cm)。一般来说,纤维的电阻率越大,表明该种纤维的导电性能越差,绝缘性越好。由于纤维截面积不规则的原因,通常不用纤维的体积电阻来表示纤维的导电性能,而是常用质量比电阻来反映某种纤维导电性能的好坏更为准确。
质量比电阻ρm,在数值上等于纤维试样长为1cm和质量为1g时所测得的电阻值,单位是欧姆·克/厘米2(Ω·g/cm2)。有时,也可以用纤维材料的表面比电阻来反映纤维的导电性能,表面比电阻在数值上等于纤维材料表面形成的宽度和长度都等于1cm时所测得的电阻值,表面比电阻的单位是欧姆。生产实践证明,相比较而言,质量比电阻是反映纤维导电性能比较客观、准确的物理量。
在生产实践中,发现在相对湿度相同的一般大气条件下,各种纤维素纤维的质量比电阻都比较接近,表明其导电性能基本一致,而蛋白质纤维的质量比电阻要大于纤维素纤维的,也就是说,其导电性能不如前者,同时,蛋白质纤维之间的质量比电阻也有很大差异。当相对湿度较低时,也就是纤维含水量很低时,纤维的质量比电阻变化很小,尤其是羊毛纤维,几乎没有变化。合成纤维由于内部分子结构的原因,吸湿差,所以,一般质量比电阻都很高。在相对湿度为80%以下时,每增加10%的相对湿度,涤纶的质量比电阻大约会以10倍的速度下降;相对湿度超过80%之后,其质量比电阻下降的速度更快,表明其导电性能增强,绝缘性能减弱。纤维的质量比电阻,与绝大多数半导体材料一样,当温度升高时,其质量比电阻值下降。
在生产实践中,人们还发现,天然纤维的质量比电阻,会随着周围环境的温度以及自身的含水量的不同而变化。毛混纺的汽车内装饰材料,在后处理过程中,处理液中盐(如NaCl)的含量增加,产品的质量比电阻就会明显下降。经过蒸馏水洗涤后的棉混纺内装饰材料,其质量比电阻明显增大。这就说明纤维材料的漂白或染色,都能改变电解质的含量,使纤维的质量比电阻发生变化,尤其是合成纤维表面整理,极容易改变其自身的质量比电阻值。有资料表明,用适当的抗静电剂对合成纤维进行表面处理,其质量比电阻可减小到原来值的万分之一,由此可见,在汽车内装饰材料的生产加工过程中,纤维的导电性能直接影响材料的技术性能。几种常用纤维和纱线的质量比电阻见表2-10。
表2-10 几种常用纤维和纱线的质量比电阻

3.静电电位 如前所述,纤维的表面形状决定其摩擦系数的大小,影响着纤维成网、成纱的纤维间抱合力,摩擦系数越大,纤维间的抱合力越大,成网、成纱强力越高,加工的汽车内装饰材料的力学性能就越好。然而,由于纤维表面状态的不光滑性,也给其生产加工带来了许多麻烦,尤其是化学纤维,其介电性能非常好,也就是说其质量比电阻很高,当开松混合梳理时,纤维与纤维之间的摩擦,纤维与机件间的摩擦,都会产生大量的静电,形成静电电荷的逐渐积聚,从而严重地影响了纤维的成网、成纱质量的均匀性。为了减少静电现象,确保纤维成网、成纱均匀性,常常利用纤维的吸湿性,在纤维加工过程中,施加适量的纤维表面活性剂、抗静电剂或水。纤维吸湿后,其自身的质量比电阻下降,表面活性剂和抗静电剂可以在纤维表面形成光滑防护膜,减小了纤维的摩擦系数,确保了生产加工的顺利进行,有时将高吸湿纤维与静电较大的纤维混合使用,也可以减轻静电现象的发生。例如,早期的毛锦混纺汽车内装饰材料,利用锦纶的耐磨性,满足汽车内装饰材料的耐磨性能要求,利用羊毛的吸湿性,克服了锦纶在加工过程中的静电问题,同时提高了产品的质量档次。如果在生产内装饰材料时,选择两种正负电荷极性相差较大的纤维,例如选择锦纶和腈纶混合,在生产加工过程中,就会产生极大的静电电荷积聚,从而导致无法进行生产。一般来说,要选择两种纤维的电荷极性比较接近的相混合,才能优势互补,还不会给生产加工带来不必要的静电麻烦。表2-11给出了各种常用纤维静电电位序列排布。
表2-11 几种常用纤维静电电位序列排布

从表2-11中可以看出,羊毛纤维的正电荷极性最强,原因是羊毛纤维的表面呈鱼鳞片状,相互摩擦极容易产生正电荷,所以具有最大的正极电荷。锦纶是聚酰胺熔融聚合而成的,其分子内部结构,决定了锦纶自身具有较高的正电荷极性,而丙纶则截然不同,聚丙烯纤维,是由不饱和碳水化合物组成的烯烃纺丝而成,其分子内部结构决定了丙纶的正电荷极性很小,负电荷极性很大,所以,在加工汽车内装饰材料的生产过程中,必须了解和掌握这些基础知识,才能更好地利用各种纤维的特性,开发理想的材料,满足汽车用纺织材料的各种功能性要求。
九、热学性能
纤维的热学性能也是纤维的一种非常重要的特性,它直接决定着该种纤维在材料加工中的应用,也直接影响着汽车内装饰材料模压组件的生产工艺,又影响着产品质量和应用性能。要研究汽车内装饰材料的舒适性,必须以纤维的热学性能为基础,掌握各种纤维的比热、导热系数、热定型温度、热收缩率、热损失率、阻燃性、软化点、熔点、分解点和玻璃化温度等,才能够充分利用各种纤维的热学性能,开发研制出符合汽车设计师要求,令汽车制造商和消费者易于接受的理想的汽车内装饰材料。
1.比热 纤维是一种热敏感材料,温度和湿度的变化,都会引起纤维性能的变化。通常把1g纤维材料,在温度每变化1℃的条件下,所吸收或放出的热量,称作该种纤维的比热,常用单位为J/(kg·℃)。生产实践证明,在不同的温度条件下,各种纤维的比热值是不同的,在100℃以下,温度对各种纤维材料的比热变化影响不大;当温度超过100℃,温度对各种纤维材料的比热值产生极大的影响,因此,在汽车内装饰材料模压组件加工过程中的工艺参数确定,必须考虑这一因素。表2-12给出了生产汽车内装饰材料几种常用纤维的比热值。
表2-12 几种常用纤维的比热值

除温度影响纤维材料的比热外,湿度也直接影响各种纤维材料的比热,水的比热值是4.186J/(kg·℃),是各种纤维材料比热的2~3倍,因此,各种纤维吸湿后,其比热都会相应地增大,这是由于纤维吸湿后,纤维与水的混合物共同产生比热,所以,在高温的夏天,汽车座椅面料吸汗后,放出的热量会更多,使司乘者感觉不舒服,因此,必须清楚纤维材料热学性能对汽车的内装饰材料舒适性的重要性。表2-13给出了各种纤维材料比热随温度升高而变化的测试结果。
表2-13 几种常用纤维在不同温度下的比热变化
单位:J/(kg·℃)

2.导热系数 纤维是一种多孔性材料,纤维内部和构成织物的纤维之间都存在着大量的孔隙,孔隙内可充满大量的空气。如棉纤维具有中腔,中腔大小由棉花的生长期决定,同时中腔的大小直接影响棉纤维的孔隙效果,决定着棉织物的保暖、隔音、隔热效果。随着化学纤维生产科技水平的不断提高,多孔中空纤维的应用量逐渐增加,尤其是在汽车内装饰材料的应用上,受到汽车设计师和汽车制造商的一致认可。因为多孔纤维材料,具有较高的导热系数,使汽车的内装饰材料具有良好的舒适性。通常把表面温差为1℃时,1h内通过1m2的纤维材料传导热量的焦耳数,称作导热系数,单位为J/(m·℃·h)。导热系数越小,表明该种纤维材料的导热性能越低,它的热绝缘性或保暖性越高。静止的空气导热系数最小,也是最好的热绝缘体,因此,加工汽车座椅靠背和坐垫时,采用多孔中空高弹涤纶,就是利用多孔中空纤维的孔隙作用,储藏大量的静止空气,保证座椅的舒适性。一般水的导热系数比较大,是纤维材料的十倍左右,所以当纤维材料吸湿后或回潮率增大后,其导热系数必然增大,保暖性、隔音、减震性下降;相反回潮率降低,纤维材料的导热系数减小,其保暖性、热绝缘性能相应提高。实践证明,各种纤维材料的导热系数,也随环境温度的波动而变化,温度高时,纤维导热系数增大,温度低时,纤维导热系数减小。表2-14给出了生产汽车内装饰材料几种常用纤维的导热系数。
表2-14 几种常用纤维的导热系数(在室温20℃条件下的测定结果)

3.耐热性能 纤维的耐热性能是由其内部结构所决定的,同时也与其成熟度和聚合度有关。在天然纤维中,同是纤维素纤维,棉纤维的耐热性能就好于亚麻、黄麻、洋麻和苎麻纤维,因此,在加工毛麻和毛棉混纺汽车内装饰材料的过程中,产品进行后处理时,工艺参数的确定,就要依据棉麻的耐热性不同来进行考虑,既要达到定型效果,又不损伤构成织物的纤维强力。黏胶纤维同样也属于纤维素纤维,可它的耐热性能也好于各种麻纤维,当黏胶纤维受热到175~180℃时,其强力仅下降5%~8%;麻纤维在同样的温度条件下,强力损失已达到30%~35%。蛋白质纤维的耐热性能,比纤维素纤维的要差,同是蛋白质纤维,其耐热性能也不相同。相比较羊毛纤维的耐热性能最差,当加热到100~110℃时,颜色变黄,强力下降25%~30%,蚕丝在同样的条件下,纤维强力只有微弱的变化,强力下降5%~6%。羊毛纤维的耐热性能,决定了原毛洗毛时的洗液温度不能高于45~50℃,烘干温度不能高于70~75℃,同样,蚕丝缫丝温度不能高于105~110℃。
对于化学纤维的耐热性能,各种不同纤维之间存在着很大的差异,从而影响了不同纤维在汽车内装饰材料中的应用。在不同温度条件下,化学纤维呈现出三种状态:玻璃态、高弹态和粘流态。当化学纤维在受热条件下,由玻璃态逐渐向粘—弹状态转化时,如果继续升温,会使其熔融。通常把某种纤维熔点以下20~40℃的一段温度,称作该纤维的软化点温度,天然纤维不存在软化点温度,其熔点高于分解点,在高温作用下,纤维素和蛋白质纤维不熔融,只能分解或炭化。表2-15给出了汽车内装饰材料生产中几种常用纤维的耐热性能。
表2-15 几种常用纤维的耐热性能

化学纤维在不同温度条件下,各种纤维会产生不同程度的收缩,通常把化学纤维受热时产生的收缩现象称作热收缩。化学纤维的热收缩特性,直接影响着汽车的内装饰材料模压组件的生产工艺及产品质量。一般锦纶和涤纶的热收缩,在沸水中和饱和蒸汽中基本接近,但是在干热空气中,涤纶的热收缩要比锦纶的大80%~100%。一般来说,同一种纤维、长丝和短纤维在同一条件下,其收缩率也不相同。锦纶长丝和涤纶长丝在沸水中的热收缩率一般为6%~10%,而锦纶和涤纶短纤维在沸水中的热收缩率只有0.5%~1.0%。同一种化学纤维在不同的热处理条件下,其反映出来的热收缩率也不一样,例如:锦纶在沸水中的热收缩可达到1.0%以上;在干热空气中的热收缩率更高;可是在饱和空气中,几乎不产生热收缩。涤纶也如此,在沸水中热收缩率在1.0%左右;可在干热空气中收缩率可高达2.5%左右;而在饱和空气中却不产生任何变化。涤纶的这种耐热性能,使其在汽车内装饰材料模压组件的加工中得到了广泛应用,而且具有最强的竞争优势,使其在汽车内装饰材料的应用量与日俱增。表2-16给出了汽车内装饰材料生产中常用的几种纤维在不同条件下的热收缩率。
表2-16 几种常用纤维在不同条件下的热收缩率

涤纶在汽车内装饰材料的生产加工中的应用量越来越大,除了从原料成本方面考虑外,与其本身的各方面性能也有着直接关系。涤纶的耐热性,在常用的纤维中是比较好的。生产实践证明,当涤纶在150℃条件下加热100h以上时,其颜色不产生任何变化,单纤维强力损失为20%~30%;在同样温度条件下,热处理1000h以上,颜色也只是产生微弱的变化,其单纤强力损失也只有40%~50%。相比之下,丙纶和聚乙烯纤维,虽然原料成本低于涤纶,但耐热性能较差,所以,在汽车内装饰材料的生产加工中的应用量受到一定的限制。
从耐热性能的角度看,腈纶的耐热性能比较适合汽车内装饰材料的需要,它的耐热性能与涤纶相接近,尤其在沸水中和饱和蒸汽状态下,其热收缩率与涤纶的基本相同,在短时间内进行100~110℃热处理,单纤维强力损失很小,只有5%~7%,由此可见,纤维的热学性能,不仅使其在不同的温度下,不同条件处理过程中,热收缩率不同,单纤维强力损失也有很大差异。这些热学性能都对汽车内装饰材料的生产加工有着决定性的影响,不仅影响工艺参数的确定,也影响最终产品的技术性能。表2-17和表2-18分别给出了汽车内装饰材料生产中几种常用纤维在不同条件下的强力损失和热定型方式及参考温度。
表2-17 几种常用纤维在不同条件下的强力损失

表2-18 几种常用纤维的热定型温度

4.阻燃性能 作为汽车用纺织材料,其所采用纤维必须具有阻燃性,否则,就要通过后处理手段来增强材料的阻燃性能。一般来说,纤维素纤维与腈纶是易燃品,燃烧速度较快;毛纤维、涤纶、锦纶、聚乙烯纤维和丙纶等,是可燃的,容易燃烧;而芳纶、芳砜纶是难燃的,离开火焰自行熄灭;玻璃纤维是不燃的,与火焰接触也不会发生燃烧,所以被广泛用于汽车工业。极限氧指数是用来表示阻燃性的一项指标,是指材料维持燃烧所需要的最低含氧量体积百分数。极限氧指数越高,表明该种纤维阻燃性能越好,相反,极限氧指数越低,阻燃性能越差。表2-19给出了几种常用纤维的极限氧指数。
表2-19 几种常用纤维的极限氧指数

5.吸热能力 各种纤维常以不同结构形态,用于汽车的隔热层和保暖层。隔热层和保暖层的作用,不仅仅是纤维作用的结果,也是纤维、空气和水的混合物共同作用的结果。热量在隔热层和保暖层传递过程中,不但有纤维自身的传导,也有热的对流和辐射。通常测得的各种纤维材料的导热系数,实际上是纤维、空气和水分混合物的导热系数。水的导热系数是纤维材料的十倍,而静止空气的导热系数很小,因此,通常测得纤维材料的导热数据能够反映某种纤维的热力学性能。涤纶、锦纶是汽车用纺织材料中最常用的纤维,它们都属于热塑性纤维,遇热后,就会吸收热量,高温时就会出现熔融;而天然纤维和黏胶纤维在受到热的作用时不软化、不熔融,在温度过高时即分解或燃烧。生产实践证明,通常情况下,使1g重的锦纶或涤纶熔融所需的热量,仅为使1g重棉纤维或毛纤维进行分解所需热量的30%~50%,因为棉毛的回潮率远高于锦纶和涤纶的。使一种纤维熔融或分解,必须蒸发掉全部的水分,水的比热又是纤维材料的2~3倍,棉毛纤维吸湿性强,体内所含水分多,因此分解难度大。而锦纶和涤纶的导热系数都大于棉毛纤维,所以锦纶和涤纶遇高温易熔融,而棉毛不易吸热而分解,这将直接影响汽车内装饰材料的生产工艺。在干燥状态下,各种纤维的比热一般相差不大,吸收热量差异也很小。当环境温度逐渐上升,从50℃开始,锦纶和涤纶熔融或棉毛纤维分解所吸收的热量相差很大,这个特性对汽车的内装饰材料的加工性能影响很大。表2-20给出了从50℃开始至天然纤维分解或合成纤维熔融所需吸收的热量。
表2-20 几种常用纤维的吸热能力

注温度范围为50~250℃
十、化学稳定性
一种纤维的化学稳定性,是指当其遇到各种化学试剂时所反映出来的特性变化。如果一种纤维与各种试剂接触,不产生形变、色变,强力和伸长也不变化,则称该种纤维具有良好的化学稳定性,反之,称其化学稳定性不好。在汽车内装饰材料的生产加工过程中,尤其是进行各种功能性整理,要使用的各种酸、碱、盐、染料、试剂、催化剂、添加剂、活性剂等,都具有很强的化学腐蚀作用,如果一种纤维的化学稳定性不好,经过加工处理后,就很难满足汽车用纺织材料技术性能要求,绝大部分酸、碱、盐都会使纤维变色,单纤维强力损失,伸长变小,同时发生形变,这就直接影响了汽车的内装饰材料的最终产品的质量和性能,因此,必须了解和掌握各种常用纤维的化学稳定性。
例如,棉纤维耐碱性好,就可以利用这一特性,采用碱煮法对其进行漂白处理,达到汽车内装饰材料所需的清洁性和白度及卫生标准要求。有时为了改善汽车内装饰材料产品的外观,可以利用碱性材料,对棉纤维进行丝光处理,赋予棉织物内装饰材料以特殊的光泽,增加产品的高档感。
锦纶从耐磨角度考虑,是汽车内装饰材料生产的首选原料,但是,锦纶遇到强酸后,单纤维强力下降,一定要控制好各种染料、试剂和活性剂中酸的浓度,在低酸浓度条件下,锦纶单纤维强力只损失5%~10%。相对而言,涤纶的耐酸性比较好,但是涤纶耐碱性较差,接触碱液后其纤维强力损失也很大。所谓化学稳定性,耐酸或耐碱,都是有相对条件的,并不是在任何条件下,纤维都具有良好的化学稳定性。正是由于涤纶的化学稳定性相对好于锦纶、黏胶和丙纶,所以,从化学稳定性方面考虑,涤纶又成为汽车内装饰材料生产的理想原料。在内装饰材料中,涤纶具有较强的竞争力和生命力。表2-21给出了几种常用的纤维的耐化学稳定性测试结果。
表2-21 几种常用纤维的耐化学稳定性

十一、光学性能
光泽是汽车内装饰材料的一个非常重要的技术指标,光泽的明暗、鲜活对轿车内部空间影响极大。光泽会给消费者带来心理上的舒适感、明亮感、空间扩大感。光泽的强弱,很大程度上直接影响着司乘人员的心情,影响他们在临时办公室和游动家居条件下的生活质量。根据光学的基本原理,当光线作用到汽车内装饰材料表面时,光线会在纤维与空气的界面上产生反射和折射,折射光线完全取决于该种纤维的表面状态和纤维内部结构性能,也就是说,取决于纤维的光学性能。一部分折射光被纤维吸收转变成其他形式的能量,另一部分折射光在到达另一个界面时,同样再产生反射和折射。因此说,汽车内装饰材料光泽的强弱,主要是由构成汽车内装饰材料的纤维表面对光的反射状态所决定的。如果纤维表面光滑一致,纤维彼此顺直平行,投射到纤维与空气界面的光线,将在一定程度上沿一定角度被反射,形成较强的反射光,从而反映给人们的视觉是该汽车内装饰材料明亮感强、光泽好,如果纤维的表面粗糙不平(如羊毛),纤维排列顺直平行度差,反射光就会以不同角度形成漫反射,汽车内装饰材料表面的光泽就会显得暗淡。
化学纤维的截面形状千变万化,然而,纤维的截面形状恰好是决定某种纤维光学性能的关键,也是影响汽车内装饰材料光泽的重要因素。生产实践证明,圆形截面的纤维材料,有着良好的反光性,会使汽车内装饰材料的表面光泽增强,例如,对棉纤维汽车内装饰材料进行丝光处理的原理,就是通过碱煮的作用,使棉纤维膨胀,天然转曲减少,截面趋近于圆形的结果。化学纤维利用异形截面,也可以改变自身的反光性,从而增强汽车内装饰材料的表面光泽,例如,三角形截面的化纤长丝具有金属般的光泽,丫形截面的化纤长丝的光泽会比三角形长丝的更强。一般情况下,三角形截面纤维的光泽优于圆形截面纤维,纤维的反光性,反映了纤维的内部结构、表面形状及纤维的品质,从而决定了汽车内装饰材料的光泽。
用来反映纤维光学性能的物理量主要有折射率和光照损失。
1.折射率 根据光学原理,当部分光线进入纤维内部后,由于纤维的特殊结构,它是一种正晶体,使折射光线分解成振动方向垂直的两束折射光,而且都是偏振光,即双折射效应(double refraction)。其中一束折射光遵守折射定律,光在纤维内部的传播速度较快,折射率不随方向而变化,折射率较小,它的振动面与光轴呈垂直状态,所以通常此条折射光线被称作寻常光线(ordinary light),折射率用n⊥表示。而另一条折射光线,则不遵守折射定律,光在纤维内部的传播速度较慢,折射率随光线的变化而变化,它的振动面则与光轴呈平行状态,所以通常把此条折射光线称作非寻常光线(extraordinary light),折射率用n||表示。纤维的折射率,取决于它的双折射率效应的大小,即两条折射光线的折射率的差值。表2-22给出了汽车内装饰材料生产中几种常用纤维的双折射率。
表2-22 几种常用纤维的双折射率

从表2-22中可以看出,纤维的折射率范围为1.5~1.6。只有涤纶例外,其非寻常光线折射率大于1.6,寻常光线折射率为1.537,涤纶双折射率为纤维之最,达到0.188。纤维双折射率的大小,除内部结构因素外,与其分子的取向度,大分子排列的整齐度,大分子主链的曲折性以及主链上侧基数量有着直接的关系。一般情况下,纤维大分子排列整齐度越高,纤维的双折射率就越大;纤维大分子排列紊乱时,其纤维的双折射率等于零。如果纤维大分链上的侧基数量较多,可能会导致纤维的双折射率为负值。纤维大分子的主链越曲折,其双折射率越低,纤维分子的取向度越高,其双折射率越高。纤维的折射也会影响其织物的光泽。
2.光照损失 纤维的耐光性能直接影响着汽车内装饰材料的品质和使用寿命,纤维在日光的直射下,会产生不同程度的裂解,在日光和大气的共同作用下,从而降低了纤维的强度,造成纤维不同程度的强力损失。光化裂解作用有时会使纤维大分子链的平均长度变短,光化裂解作用的强弱,取决于光照强度、光照时间、紫外线波长、纤维的内部结构以及试验相关条件,表2-23给出了汽车内装饰材料生产中,几种常用纤维在正常日照强度条件下,随日晒时间的不同,纤维强力损失的统计结果。
从表中可以看出,腈纶耐光性能最好,在相同日照时间内,其强力损失只是纤维素纤维的一半,这是由于纤维素纤维的内部结构所决定的。在汽车内装饰材料生产加工几种常用纤维中,锦纶的耐光性较差,光化裂解作用较强,纤维强度损失较大。生产实践证明,二氧化钛(TiO2)消光剂只能加快光化裂解反应速度,使纤维的耐光性更差,所以,汽车内装饰材料生产中应尽量少用无光丝,许多染料、助剂、活性剂,也会不同程度地影响各种纤维的光化裂解作用,因此,在汽车内装饰材料的生产过程中,尽量减少消光剂的使用,合理选择染料和各种助剂等。
表2-23 几种常用纤维在日照时间相同和不同的条件下强力变化结果

涤纶从耐光性的角度考虑,也是一种较为理想的汽车内装饰材料的使用原料。从表2-23可知,涤纶的耐光性与棉纤维和黏胶纤维相接近,但好于锦纶,大量试验和检测结果证明,涤纶具有一个特殊性,它可以借助汽车玻璃滤掉大多数有害的紫外线,窗玻璃的过滤结果使涤纶的光化裂解作用明显减弱,氧化裂解反应极其微弱,汽车内部涤纶的耐光性几乎与腈纶相同,所以,涤纶具有良好的抗紫外线性能,这也是汽车内装饰材料生产中涤纶需求量越来越大的一个重要原因。几种常用纤维在不同条件下的耐光性能见表2-24。
表2-24 几种常用纤维在不同条件下的耐光性能


十二、耐磨性能
纤维和纱线的耐磨性能直接决定着汽车内装饰材料的耐磨性能,而影响纤维和纱线耐磨性能的因素很多,也比较复杂。影响纤维耐磨性能的主要因素有纤维大分子的内部结构、大分子主链键能强度、大分子链的柔曲性、纤维的聚合度、纤维的取向度、纤维的结晶度、结晶的均匀性、纤维的玻璃化温度、纤维的表面光滑度、强度、拉伸急弹性恢复率、拉伸断裂比功、恢复功系数等。
影响纱线耐磨性能的因素更多,除上述影响纤维耐磨性的因素外,还有长丝纱和短纤纱的差异,单纱和股线之间的区别,纤维混合类型及比例的不同,纱线号数、捻度、捻回、捻系数等因素。同一种纤维和纱线,制成汽车内装饰材料的生产工艺方法、织物组织结构不同,纤维和纱线所反映出来的耐磨性能,都存在着很大差异,然而,耐磨性能对汽车内装饰材料而言,是一个硬性指标,因此,学习了解和掌握常用纤维和纱线的耐磨性能,对研制开发和应用汽车内装饰材料,意义非常重大。
一般来说,纤维大分子的主链键能强度越大,大分子链的柔曲性越好,纤维的聚合度越高,取向度越高,成熟度越好,结晶区均匀,结晶度适当,生产汽车内装饰材料的模压组件工艺温度越接近某种纤维的玻璃化温度,该种纤维的耐磨性能就越好,用其加工成的汽车内装饰材料的耐磨性能就越强,使用寿命就越长。
生产实践证明,纱线的捻度大,号数小,捻系数高,其纱线及织物的耐磨性能就好,用其加工的汽车内装饰材料使用寿命就相对较长。
1.磨损减细率 汽车内装饰材料生产中,几种常用纤维在张力为0.74gf的条件下,试样平均纤维线密度为3.33tex,绕过转轴四分之一周,转轴表面磨料为1200目金刚砂,磨损28转时,各种纤维的减细率见表2-25。
表2-25 几种常用纤维磨损减细率

从表2-25中可以看出,涤纶和锦纶耐磨性能较好,同等条件下涤纶减细率只有1.7%;腈纶减细率为13%,是涤纶和锦纶的7~8倍;毛纤维磨损最为严重,在同等条件下,减细率达到了27.7%,是涤纶和锦纶的15~16倍,是腈纶的一倍多,所以,毛纤维必须与其他纤维混合使用,才能满足加工汽车内装饰材料的要求。
2.磨断转数 减细率可以反映出一种纤维在特定试验条件下的耐磨性能,磨损量(一般磨损量多用减细率来表示)更能准确地反映出纤维和纱线的耐磨性能。一般磨损寿命常用纤维和纱线被磨断的转数来衡量。表2-26给出了汽车内装饰材料生产中,几种常用纤维在试验条件拉伸张力为13.23cN/dtex情况下的磨损寿命。
表2-26 几种常见纤维的耐磨损寿命

从表中可以看出,锦纶的耐磨性能最好,涤纶次之,丙纶第三,远远大于其他纤维。
3.磨损量 表2-27给出了汽车内装饰材料生产中,几种常用纤维和纱线的磨损量测试结果。
表2-27 几种常用纤维和纱线的耐磨损性能

从表中可以看出,长丝纱的耐磨性能好于同类纤维的短纤纱,短纤单纱的磨损量是同种纤维长丝的1.6~4.8倍;双股线的磨损量都大于单纱,一般在1.5倍左右;从磨断转数看,同一原料双股线的耐磨性好于单纱。涤纶粗梳双股线的磨断转数是单纱的10~11倍,这是股线捻度和捻系数作用的结果,由此可见,纤维和纱线的耐磨性能,是汽车内装饰材料生产加工中的一个非常重要的原料技术指标。