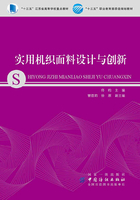
任务三 白坯织物生产工艺
项目一 确定白坯织物生产工艺流程
1.经纱准备 络筒→分批整经→浆纱→穿经→织造→验布→修补→后整理(烧毛、退浆、煮练、丝光、染色、印花、拉幅定型、预缩、压光)
2.纬纱准备 络筒→(定捻、并线、卷纬)
注:弹性纱、强捻纱要经过定捻工序,股线要并线,有梭织机要卷纬。
白坯织物适宜量大面广的产品生产,具有成本低、质量好的特点。
项目二 白坯织物生产工艺参数设计
一、白坯织物工艺参数设计
白坯织物生产工艺参数包括络筒、分批整经、浆纱、穿经、织造等工序的参数,各工序工艺设计(续前设计案例)见表1-7。
表1-7 CVC 14.6tex/14.6tex府绸(总经根数6488根,公称坯长40码)




二、各工序参数设计说明
1.络筒张力
(1)络筒张力大,则卷绕密度大,有利于成形良好,但络纱张力大,断头增加;络纱张力小,筒子松软,不利于成形良好,卷装容量小。
(2)络筒张力通常为单纱断裂强力的8%~12%。现代络筒机张力装置见图1-6。
(3)普通络筒机圆盘式络筒张力配置参数见表1-8。

图1-5 自动络筒机

图1-6 现代络筒机工艺部件

络筒工序
表1-8 普通络筒机圆盘式络筒张力配置参数

2.电子清纱器清纱工艺参数设置 电子清纱器(图1-6)的清纱工艺参数设置(图1-7)要点如下。

图1-7 电子清纱器清纱工艺参数设置
(1)短粗节:纱疵截面增量在+100%以上、长度在1~8cm,称为短粗节,分为16级(A1、A2、A3、A4、B1、B2、B3、B4、C1、C2、C3、C4、D1、D2、D3、D4)。生产中常见短粗节为B1级和B2级。
(2)棉结:纱疵截面增量在+100%以上、长度在1cm以下的纱疵。
(3)长粗节:纱疵截面增量在+45%以上、长度在8cm以上的纱疵。分为F级、G级,生产中常见短粗节为G级。
其中,纱疵截面增量在+100%以上、长度在8cm以上的E级纱疵称为双纱。
(4)长细节:纱疵截面增量在-30%~-75%、长度在8cm以上的纱疵。长细节分为4级(H1、H2、I1、I2),生产中常见的有害纱疵为I2级。
3.机械板式清纱器的隔距 传统络筒机采用机械板式清纱器(图1-8)的隔距设置:
δ=1.75×d0,这里δ(mm)为板间距,d0(mm)为纱直径。
对于棉纱:,因而
;
对于棉股线:,因而
。

图1-8 机械板式清纱器
4.卷绕密度
(1)筒子的卷绕密度直接影响到筒子的卷装容量,卷绕密度小,则卷装容量小,即卷装长度小,同时易造成筒子过于松软,成形不良;卷绕密度大,则卷装容量大,但过大的卷绕密度会导致退绕张力增大,整经断头增加。
(2)筒子卷绕密度间接反映络纱张力的高低,络纱张力高,则卷绕密度大。
(3)络纱线速度高,则卷绕密度大。
(4)纱线线密度小,则卷绕密度大。
(5)纤维弹性好、表面光滑,则卷绕密度大,如涤棉纱的弹性较高,卷绕密度较纯棉纱高10%~15%。
(6)棉纺织生产中,整经筒子的卷绕角为30°,染色用的松式筒子卷绕角为55°左右,故后者的卷绕密度较前者小。
(7)整经用的筒子,卷绕密度见表1-9。
注:股线较单纱卷绕密度高10%~20%,涤棉等化纤纱较纯棉纱卷绕密度高约10%。
表1-9 筒子卷绕密度

1.整经配轴 分批整经机(图1-9)配轴工艺计算如下,假设总经根数为6488根,筒子架容量为640根。
(1)初算整经轴数与修正轴数。

修正轴数为11。


图1-9 分批整经机

整经
即每轴589根,余0.82×11(轴)=9(根),将其平均分配于其中的9轴之上。
(3)修正配轴:590×9(轴)+589×2(轴)。
2.经轴卷绕密度 经轴卷绕密度设置见表1-10,在保证下道工序经轴退绕轻快均匀的情况下,经轴的卷绕密度应较筒子的卷绕密高10%~20%。
表1-10 分批整经经轴卷绕密度

经轴卷绕密度的影响因素如下。
(1)卷绕张力:卷绕张力由筒子架上张力盘的加压力和经纱与导纱瓷柱的包围角决定,卷绕张力越高,则卷绕密度越大。
(2)整经机的线速度:整经机整经的线速度越高,则相应整经张力越高,卷绕密度越高。
(3)经纱的线密度:纱线的线密度越低,则卷绕密度越高。
(4)纤维材料:涤棉纱表面较纯棉纱光滑且弹性较好,因而卷绕密度较纯棉纱大约10%。
浆纱机(图1-10)浆纱工序主要设计说明如下。

图1-10 浆纱机

浆纱
1.浆料 黏着剂主要有淀粉类、PVA类、聚丙烯酸类三大类浆料,此外还有CMC、聚酯浆料等。
(1)淀粉类:淀粉有天然淀粉和变性淀粉两类。
①天然淀粉应用较为普遍的是玉米淀粉和马铃薯淀粉。玉米淀粉浆液浸透性、耐煮性好,浆膜强力高,但浆膜较硬脆;马铃薯淀粉的最主要优点是成膜性好,但耐煮性较差,黏度不稳定。根据相似相容原理,天然淀粉主要用于纤维素纤维(如棉、麻、黏胶)上浆。
②变性淀粉:有酸化淀粉、氧化淀粉、醚化淀粉、酯化淀粉、接枝淀粉。共同特点是高浓低黏、流动性好、浸透性好,黏附性提高,不易凝胶(酸化淀粉除外),此外还有特殊用途的交联淀粉。
酸化淀粉见表1-6项目3所述;醚化淀粉应用最多的是羧甲基淀粉CMS,主要特点是水溶性好,容易退浆,但是浆膜较柔软,容易起毛,一般与其他浆料复配使用;酯化淀粉含有酯基团,对聚酯纤维黏附力改善,主要有磷酸酯淀粉和醋酸酯淀粉;接枝淀粉具有疏水性共聚物,对疏水性的聚酯纤维有较强的黏附性,是新一代淀粉;交联淀粉黏度较大,可以形成较厚的浆膜,有利于被覆毛羽,适合麻、毛织物上浆。
(2)PVA类:PVA类主要有PVA1799、PVA1788、PVA205及PVA0588等种类。
①PVA1799:聚合度为1700,醇解度为99%。浆膜强力、耐磨性、耐屈曲性高于其他几种,应用较广,但是常压煮沸2小时以上才能溶解,分纱阻力大,细特高密织物上浆在分绞区容易造成纱线断头。
②PVA1788:醇解度为88%,对聚酯纤维的黏附性高于PVA1799,易溶解,浆液易起泡。
③PVA205:PVA205是日本可乐丽公司生产的部分醇解产品,醇解度为93%,聚合度为500,混溶性好、分纱阻力小,一般和PVA1799混合使用,降低分纱阻力。
④PVA0588:聚合度为500,醇解度为88%,性能与PVA205相近。
(3)聚丙烯酸酯:见表1-7工序项目3。
(4)浆液配方:
浆料总重(kg)=PVA+固体丙烯酸酯+酸化淀粉+助剂(SLMO96平滑剂+NL-4防腐剂)=37.5+20+40+3+0.4=100.9
黏着剂复配比例近似为:PVA:固体丙烯酸酯:酸性淀粉=40%:20%:40%,即化学浆(PVA+聚丙烯酸酯):淀粉浆=6:4,符合涤棉经纱的“相似相容”浆料复配原则。PVA可以增加低特纱浆膜耐磨性,浆膜强力高、成膜性好,有利于被覆涤棉纱较多、较长的毛羽,淀粉浆液浸透性好,对棉纤维黏附性较好,丙烯酸酯可以增加浆纱弹性,降低浆纱分绞阻力。
2.上浆率
(1)上浆率:上浆率是指上浆后浆料的干重对经纱干重的百分率。
①上浆率直接决定上浆后浆纱强力、伸长、弹性及耐磨性,最终决定织造效率的高低。
②上浆率过低会影响浆液对经纱外表面毛羽的被覆与浸透效果,进而影响织造时的开口清晰度,由此导致三跳(跳花、跳纱、星跳)、纬缩次布,最终影响产品质量(下机一等品率)。
③上浆率高低将影响浆料成本和染整工序的退浆成本。
(2)制订依据:上浆率根据纱线线密度、织物组织、织物密度、织机速度而定。
①低特织物经纱上浆率较高,以增加经纱耐磨性和强力。
②织物组织循环内交织点越多,则织造时经纱所受到的织机开口、打纬引起的摩擦越剧烈,上浆率应越高,平纹组织>2/1斜纹组织>3/1斜纹组织>缎纹组织>小提花组织。
③织物经纬密度大,则上浆率应高,以抵御经纱间摩擦作用及打纬时钢筘对经纱的摩擦。
④织机速度越高,则钢筘对经纱的摩擦加剧,上浆率越高,基础上浆率见表1-11。
表1-11 基础上浆率

(3)生产中影响上浆率的因素。
①浆液浓度:浆液浓度是影响上浆率的决定性因素,浆液的浓度越高,上浆率越高。
②浆液黏度:浆液黏度是控制上浆率的重要手段,浆液的黏度越高,被覆上浆增加(浆膜变厚),则上浆率相应增大,同时落浆率可能增加。
③浆纱机速度:浆纱机的车速高,压浆后经纱上浆液的余留较多,上浆率较高。
④浸没辊深度:浸没辊的深度大,浸浆区长,上浆率较高,但调节浸没辊的高低位置会恶化浆纱伸长,一般使其中心位置与液面平齐。
⑤压浆辊的压力:压浆辊(图1-11)的压力越低,则压浆后浆液在纱线上的余留越多,被覆上浆越高,上浆率越高;反之,压浆辊的压力高,则浸透上浆高,被覆上浆低,即压浆后纱线上余留的浆液少,上浆率低。靠近烘房的压浆辊对上浆率起决定作用。
⑥经纱张力:经纱张力越低,经纱纤维间空隙越多,有利于浆液浸透与吸附,上浆率较高。

图1-11 压浆辊
⑦压浆辊的表面状态:压浆辊表面弹性好,有微孔,将有利于浆液的吸附及压浆后浆液的二次分配,上浆率较高。压浆辊在使用过程中,橡胶层表面会逐渐老化,弹性下降,应该每六个月到一年研磨一次,以保证上浆效果。
⑧浆液温度:一方面,浆液温度提高,浆液分子布朗运动加剧,有利于浆液浸透,对上浆率提高有积极作用;另一方面,浆液温度提高,会加速浆液分解,使浆液黏度降低,导致上浆率降低。上浆率最终结果取决于上述哪一方面占主导作用,一般后者起主导作用的情况较多。
⑨经纱的性质:经纱表面毛羽较多(如气流纺纱),有利于对浆液的吸附,上浆率较高;经纱的捻度较小,经纱结构相对松散,将有利于对浆液的吸附,上浆率较高。
⑩纤维的性质:亲水性纤维如棉、麻、黏胶纤维由于含有大量的羟基,因而根据相似相容原理,对同样含有亲水性羟基的浆料(如淀粉、PVA、CMC等)有很好的亲和性,上浆率较高;涤纶纱应该采用对其有一定黏附性的PVA、聚丙烯酸酯上浆。
3.回潮率
(1)回潮率:回潮率是浆纱中水分的重量占浆纱干重的百分率,其对织造的影响如下。
①纱线的弹性:如果回潮率过低,浆纱弹性下降,纱线将不能抵抗织造过程中的冲击、弯曲、摩擦而产生脆断头。
②浆膜性能:回潮率过高,则浆膜软,耐磨性较差,同样容易产生织造断头。
③织物疵点:回潮率过高,对棉织物来说会产生大量的布面棉球次布。
④开口清晰度:回潮率过高,经纱易粘连,开口清晰度差,易产生“三跳、纬缩”次布。
⑤浆纱回潮率过高,经纱更易产生伸长,产生窄幅长码布,且布面易发霉。
⑥对以淀粉为主的混合浆而言,回潮率过低,浆膜脆硬,被覆不牢、织造时落物率(落浆、落棉)高,恶化织造条件。
(2)制订依据:回潮率在一定程度上决定布机车间的温湿度控制范围。确定依据与范围如下。
①回潮率的大小应根据纱线原料、线密度和上浆率等情况来确定。一般黏胶纱的回潮率大,合成纤维纱较低,棉纱的回潮率居中。
②应尽量使织轴在布机车间处于放湿状态,因为过度干燥的浆纱很难在布机车间通过吸湿获得必要的回潮率。
③南方梅雨季节,回潮率应控制得低些(下偏差范围内),以避免棉球次布。
(3)控制范围:见表1-12。
表1-12 回潮率的一般控制范围

(4)生产中影响回潮率的因素。
①烘筒温度:浆纱速度一定条件下,烘筒温度越高,则回潮率越低。
②浆纱机车速:烘燥温度一定的条件下,浆纱机车速越低,则回潮率越低。
③湿加重率与上浆率:湿加重率与上浆率越高,则烘筒负担越重,回潮率越高。
④生产中采用“定温变速”法控制回潮率。
4.伸长率
(1)伸长率定义:指上浆后浆纱增加的长度相对于上浆前经纱长度的百分率。浆纱伸长率对织造效率、成布质量和生产成本有重要影响。
①织造效率:过高的浆纱伸长率将影响经纱的弹性回复性,最终增加织造断头率。
②织物缩水率:浆纱伸长率过高,织物的缩水率将增加,尺寸稳定性下降。
③布幅:伸长率过高,易出窄幅长码布。
④织物质量:伸长率将影响织物的内在质量,如服用牢度。
⑤生产成本:一方面,伸长率将影响经纱用纱量,从而直接影响产品的成本;另一方面,经纱伸长率将影响经纱弹性与织造断头率,从而间接影响生产成本。
⑥机配件的寿命:如果浆纱的伸长率控制得过高,对同种纤维材料的经纱,所需张力需相应增加,这会加速机件疲劳,使机配件寿命缩短。
总之,浆纱的伸长率反映了上浆过程中纱线的拉伸情况。伸长率过大时,纱线的弹性会损失过多,剩余断裂伸长率下降。
(2)制订原则:
①纤维材料是决定浆纱伸长率的关键因素,黏胶纱由于纤维内结晶区少,无定型区多,在张力、热、湿等作用下容易产生伸长,伸长率较大;棉纱次之;涤棉纱中的涤纶是热塑性纤维,受热收缩可抵消部分受力产生的伸长,伸长率不高;股线由于捻缩的影响伸长率最小。
②其他条件一定时,线密度较低的纱的浆纱伸长率应当较小,以保持弹性,减少织造断头,如纯棉9.7tex浆纱伸长率以低于0.8%为宜。
③应使浆纱机退绕区的各个经轴在退绕过程中的伸长彼此一致,以减少了机回丝。
④使经轴在退绕过程中(自满轴到小轴)伸长始终一致,以保持纱线原有机械性能。
(3)控制范围:浆纱伸长率一般控制标准见表1-13。
表1-13 浆纱伸长率的一般控制标准

(4)生产中影响浆纱伸长率的因素:湿、热、张力是影响浆纱伸长率的三要素。
①退绕区:指经轴与引纱辊之间的区域,将经纱从整经轴上退绕下需要一定的张力,由于经纱退绕过程中经轴的惯性回转,经纱的伸长和张力都不大。
要保证各经轴退绕张力和伸长率一致,减少了机回丝,张力和伸长的控制可以通过调节经轴气动制动带(图1-12)的制动力来控制经轴退绕阻力。
②上浆区:如图1-13所示,在浆槽区,引纱辊的表面线速度大于上浆辊,经纱处于松弛状态,以利于吸浆,浆纱伸长不大,甚至略有收缩,伸长率可能为零或者负伸长。

图1-12 经轴退绕制动装置图

图1-13 经纱在浆槽内上浆工艺流程
③预烘区(湿纱区):湿浆纱在预烘区要蒸发70%以上的水分,纱线处于“湿、热、张力”状态,张力不大,但是伸长率是浆纱过程中最大的。
④烘燥区:烘燥区的烘筒(干区)进一步烘干剩余的20%以上的水分,此区的张力逐渐增加,直到将要进入的分绞区的高值,在干烘燥区,伸长值主要取决于纱线的受热收缩和受力伸长哪一方占主导:对于纯涤和涤棉织物,受热收缩率大于受力伸长,伸长率为负值,纱片绷紧烘筒;对于棉织物,由于纱线已经烘干,纱线受力略有伸长;对于黏胶纱,纤维结晶区少,无定形区多,受力后湿伸长很大,纱片容易松弛。
⑤分绞区、卷绕区:浆纱已经烘干,受力不易伸长。
5.浸压方式 浆槽由引纱辊、浸没辊、上浆辊、压浆辊组成(图1-13),浸压方式是指上浆辊、压浆辊和浸没辊的不同组合方式。浸压方式的确定原则如下。
(1)单浸单压:对于黏胶织物、莱赛尔织物,由于其吸湿量大,容易吸浆,湿态易伸长,因而一般采用单浸单压(图1-14),以避免恶化伸长,影响后道织造过程中经纱的回弹性,导致断头率增加。
(2)单浸双压:对于低特、密度低、总经根数不多的棉型织物,如纯棉平布,采用单浸双压方式(图1-15)即可满足浆液浸透和被覆的需要。
(3)双浸双压:对于大多数棉织物和涤棉织物,一般采用双浸双压的上浆方式(图1-16),也是纺织浆纱上浆的最普遍方式。

图1-14 单浸单压

图1-15 单浸双压

图1-16 双浸双压
(4)双浸四压:对于高密厚重棉织物和高密涤棉织物,一般采用双浸四压(两浸没辊分别对上浆辊侧压)的上浆方式(图1-17)。
(5)三辊侧压(图1-18):此种方式的结构简单,挤压辊少一对,浆槽容积减小,浆液稳定,上浆均匀,起到双浸双压的效果,浆液的浸透和被覆较好;挤压道数减少,附加伸长率减小。

图1-17 双浸四压

图1-18 三辊侧压
6.含固量设计
(1)含固率确定:含固量是指浆液中浆料干重占浆液重量的百分率。含固量的计算如下:
S=C×K
(1-36)
式中,S为上浆率,C为浆液含固量,K为压出加重率。
①传统中低压上浆(一般是压浆力12kN以下):压浆辊压力较轻,压出加重率(也称压余带液率,是指浆纱出压浆辊、进烘房前增加的浆液重量相对于进浆槽前的经纱重量之比)较高,一般为120%~130%,其值主要取决于靠近烘房侧的压浆辊的压力,压力高,则压出加重率K小,若取K=125%,上浆率S=10%,带入式1-36,计算出浆液C=8%。
②现代高压上浆:在本设计(表1-6工序项目3)中,压浆力大,压出加重率较小,有利于增加浆液浸透,减轻烘房的烘燥负担,提高浆纱车速和效率,K为95%~100%,如K选100%,上浆率S=10.5%,代入式1-36,得到C=10.5%。
比较传统中低压上浆和现代高压上浆可知,为达到同样的上浆率,后者需要较高的浆液含固量(浓度),不可避免带来浆液黏度的提高,这会影响浆液浸透性。因而高压上浆,必须同时采用高浓低黏的浆料,如各种变性淀粉和化学浆等。
(2)含固率估算:调浆前应根据浆液配方和含固率值初步估算所用浆料的用量和调浆体积,计算时不能忽视浆料含水率。调浆桶、高压煮浆桶如图1-19所示。

图1-19 调浆桶、高压煮浆桶和调浆桶内部图
注:PVA含水率为8%(含固率92%),淀粉含水率为14%(含固率86%),固体聚丙烯酸酯LMA含水率约为15%(含固率约85%)。
例1:表1-7工序项目3中浆料配方含有黏着剂PVA、固体丙烯酸酯LMA96、酸性淀粉TB225等。含固率C=10%,调浆体积=750L。
注意:浆液中煮浆蒸汽凝结成的水不容忽视,尤其是冬季,一般每800L浆液会有15~20kg的蒸汽冷凝水。设计调浆配方各组分重量时,要考虑调浆工的操作方便,如国内PVA包装为12.5kg/袋。

考虑到浆料配方中含有助剂,故含固率基本符合标准。
例2:设本细特CVC织物的浆料配方为PVA:变性淀粉=30%:70%,调浆体积为80L,含固率为11%。求PVA和变性淀粉用量。
解:设PVA用量为Xkg,变性淀粉用量为Ykg,则有:
X:Y=3:7

解上述方程式,可得:X=35kg,Y=82kg。
7.浆槽黏度设计
(1)黏度设计的意义:上浆率和浆槽黏度是正相关关系,控制浆槽黏度是调节上浆率的最直接的手段。
①黏度影响浆液的浸透、被覆和浆膜厚度:浆液含固率一定时,浆液黏度低,则浆液浸透性好,浆膜薄,上浆率偏低;黏度高,上浆率高,浆膜厚度大,浆纱耐磨性和毛羽被覆好。
②浆液黏度过高,易造成压浆辊打滑,不利于浆纱操作,产生浆纱黏并、分绞区落浆多、伸缩筘撞断头,产生倒断头及浆斑次布,现代上浆采用“高浓、高压、低黏”工艺。
③黏度的现场测试采用相对黏度(单位为s),采用手提漏斗式黏度计(图1-20)测量,规定整漏斗常温水流完的时间为3.8s作为标准水值。
实验室采用绝对黏度(厘泊)指标。1cP=1mPa·s(毫帕斯卡·秒),采用回转式黏度计(图1-21)测试。

图1-20 手提漏斗式黏度计

图1-21 NDJ-79回转式黏度计
(2)浆槽黏度与上浆率的对应关系:不同线密度的织物,其浆槽黏度与上浆率的一般对应关系见表1-11。
(3)浆液黏度影响因素。
①浆料:含固量一定的条件下,黏度排序为:CMC浆>天然淀粉浆>变性淀粉浆>PVA浆。
②浆液浓度:浆液的浓度越高,则浆液的黏度也越高。
③浆纱机车速:浆纱机的车速越高,浆液使用越快,浆液循环越快,黏度较高;反之,浆纱机的车速越低,浆液烧煮时间过长,分解度高,黏度降低。
④浆液温度:浆液温度越高,含淀粉的浆液分解度高,黏度下降。
⑤浆液pH:浆液的pH高,则含淀粉的浆液分解度高,黏度易下降。
⑥用浆时间和机械搅拌:浆液使用时间过长或机械搅拌过度都会加速浆液的分解,浆液的黏度下降。
⑦蒸汽中含水:如果蒸汽含水过高,特别是在冬季,会稀释浆液,导致浆液黏度下降。
8.浆槽温度设计
(1)浆液温度设计的意义。浆液的温度会影响浆液的流动性,从而使浆液的黏度发生变化。温度高,分子运动加剧,浸透性好,不会造成表面上浆;但温度过高,会造成黏度下降,浆膜变薄,上浆率下降。
(2)浆液温度设计的原则。
①不同的纤维对浆液温度的要求有一定的差异,如棉纤维表面有油脂和棉蜡等拒水物质,浆液的温度会影响棉纱的吸浆性能,一般应在95℃以上的高温下上浆;而羊毛和黏胶纤维的经纱经热湿处理,强力和弹性都会损失,应在较低的温度下上浆(55~65℃为宜)等。
②纯淀粉浆应采用98~100℃高温上浆,低温易产生凝胶现象,从而出现浆斑次布;含PVA的混合浆上浆温度为97~99℃,不能采用100℃上浆,因为PVA分子在100℃沸腾时,浆液水分蒸发,PVA分子发生定向排列,产生浆斑次布;纯PVA浆上浆温度在60~90℃。
(3)浆液温度的影响因素。
①浆槽内蒸汽压力大小直接影响着浆液温度的高低,压力大,则浆液的温度高;压力小,则温度低。
②新浆液的不断补充也会影响浆液的温度,新浆液补充不均匀会造成温度分布不匀,应当测浆槽四角温度来调控浆液的温度。
9.浆液pH设计
(1)pH设计原则。
①浆液的pH将直接影响浆液的分解度,棉型织物上浆的浆液的pH一般控制在弱碱性范围内,碱性越高,浆液的分解越快,碱性过高时,浆液易变稀薄,容易造成轻浆;碱性过低时,淀粉粒子糊化不足,对浆液黏性有影响。
②pH对上浆性能与纱线的性能影响较大,如毛纱耐酸不耐碱,毛纱上浆的浆液应为弱酸性;而棉纱耐碱不耐酸,则其浆液宜为碱性;黏胶纱宜采用中性浆。应根据不同的纱线特性来制定浆液的pH。
(2)pH范围。
①以淀粉为主的混合浆(淀粉比例大于70%)。调浆桶为10±0.5(50~60℃定浓时);煮浆桶为8~8.5;浆纱机浆槽为7.5~8。
②以化学浆(PVA)为主的混合浆(化学浆比例大于70%)。调浆桶为8±0.5;煮浆桶为7~8;浆纱机浆槽为7~7.5。
(3)浆液的pH影响因素。
①淀粉储存时间:淀粉储存时间越久,浆料的酸份增加,pH下降,生浆浸渍时间过长或未撇黄水,会造成酸度高;若碱用量过多,则碱度过高。
②分解剂使用:淀粉浆须使用分解剂,氢氧化钠或硅酸钠用量越高,pH越高。
③上浆过程:随上浆过程的进行,浆液中的碱不断消耗,pH逐渐降低。
10.压浆力 浆槽压浆辊(图1-22)的压浆力配置分为先重后轻和先轻后重两种方式,前者强调被覆,后者强调浸透上浆。压浆辊压力由压缩空气通过气缸或者气囊作用于压浆辊上施压,气缸加压容易带来加压和施压滞后,左右压力不一致的问题,气囊加压不会产生这些问题。现代上浆采用先轻重、压浆力逐渐增加的方式,目的是将纱线中的空气逐渐挤出,增加浆液浸透性。
(1)第Ⅰ压浆辊:即经轴侧(进口)压浆辊,压强为0.25~0.4MPa。
1MPa相当于24kN(压浆辊气压表如图1-23所示),即对第一压浆辊,1MPa可以提供24kN的压力,则压浆力为6~9.6kN。

图1-22 浆纱机压浆辊

图1-23 压浆辊气压表
本设计(表1-7工序项目3)中,经轴侧压力为0.3MPa,因而压浆力=0.3×24=7.2(kN)。
(2)第 Ⅱ压浆辊:即烘筒侧(出口)压浆辊,压强为0.30~1.0MPa。
1MPa相当于40kN,即对第二压浆辊,1MPa可以提供40kN的压力。
本设计(表1-7工序项目3)中,经轴侧压力为0.5MPa,因而压浆力=0.5×40=20kN。
调整压浆辊施压操作:拉出并旋转气动调节旋钮至压力表刻度规定值,推上旋钮即可。
11.烘筒温度 一般浆纱机的烘房(图1-24)预烘区温度高,目的是使得水分大量汽化,合并区温度较低,目的是避免已经形成的浆膜因高温损伤。温度取决于纤维原料、经纱线密度、总经根数等。

图1-24 浆纱机烘燥区
对于吸湿性好、回潮率高、线密度高、总经根数多、不易烘干的经纱应该采用较高的烘燥温度,一般预烘燥温度高于120~135℃,对应的烘筒蒸汽压力为0.3~0.4MPa,合并烘干区的温度为110~120℃,对应的烘筒蒸汽压强为0.2~0.3MPa。
对于吸湿性低、回潮率小的经纱,如纯涤纶、涤棉经纱,采用较低的烘燥温度即可达到烘燥目的。
一般预烘区(湿区)温度比烘干区(干区)高10~15℃。
12.浆纱各区张力
(1)各区张力分布:如图1-25所示。

图1-25 浆纱各区张力控制
①退绕区:经轴区~M7。
②上浆区:浆槽一为M7~M6;浆槽二为M5~M4。
③预烘区(湿区):浆槽一为M6~M3;浆槽二为M4~M3。
④干纱区(烘筒烘干区+分绞区):M3~M2。
⑤卷绕区:M2~M1。
(2)各区张力(图1-26)计算:本设计(表1-7,工序项目3)中,总经根数为6488根,经纱线密度为14.6tex,根据纺纱方式、配棉品级和捻度等,确定精梳涤棉纱的比强度为12cN/tex。
①纱片重量=总经根数×特数/1000=6488×14.6/1000=95(g/m)
(1-39)
②单纱断裂强力=特数×比强度=14.6×12=175(cN)
(1-40)
③总断裂强度=总经根数×单纱断裂强度(cN)/100=6488×175/100=11354(N)
(1-41)
④各区张力=总断裂强力×依所计算纱片重量而定的各区折算系数(表1-14,本设计取平均值),涤棉纱纱片重量=95g/m。
退绕区E1张力=11354×退绕区张力折算系数=11354×3.75%=425(N)
(1-42)
上浆区E2张力=11354×上浆区张力折算系数=11354×2.25%=255(N)
(1-43)
湿烘燥区E3张力=11354×湿烘燥区张力折算系数=11354×2.75%=312(N)
(1-44)
干纱区E4张力=11354×干纱区张力折算系数=11354×9.5%=1078(N)
(1-45)
卷绕区E5张力=11354×卷绕区张力折算系数=11354×12%=1362(N)
(1-46)
表1-14 分区张力折算系数

(3)各区张力控制示意:如图1-26坐标图所示,图中实线表示控制标准值,虚线表示上限和下限值,斜剖线代表最小张力。
(4)卷绕区托纱辊对织轴的压力。
①托纱加压辊(图1-27)对织轴的压力可以调整织轴的卷绕密度。
②托纱加压辊压力=纱片重量×托纱加压辊压力折算因子
(1-47)

图1-26 浆纱机各区张力示意图

图1-27 浆纱机托纱加压辊
根据表1-15,纱片重量=95g/m,托纱加压辊压力折算因子选20,因而有:
托纱加压辊压力=95×20=1900N
表1-15 托纱辊压力折算因子

(5)浆纱机各区现场。
①退绕区:图1-28。

图1-28 浆纱机退绕区
②浆槽区:图1-11和图1-22。
③烘燥区:图1-29。
④分绞区:图1-30。
⑤卷绕区:图1-31。

图1-29 贝宁格浆纱机烘燥区

图1-30 浆纱机分绞区

图1-31 浆纱机卷绕区
⑥其他:车头工艺参数设置界面如图1-32所示。
13.浆纱墨印长度 浆纱墨印长度指织造一匹布所需经纱的长度。


图1-32 车头工艺参数设置界面
注:①自然缩率和放码损失率,平纹组织选1.5%,斜纹组织、缎纹组织和其他组织选0.8%。
表1-7工序项目3的设计中,公称匹长为40码,1码=0.9144m,经纱织缩率为8.29%(表1-6)。
②通过比较浆纱墨印长度和整理车间的坯布间墨印长度,可以测得精确的经纱织缩率。
相关计算和说明见情境一任务二项目二设计案例,补充说明如下。
1.综页数的计算 综页数不但取决于织物组织,即不同运动规律的经纱分穿在不同综页内,还要考虑综丝密度,如果综页数过少,则综丝密度过大,导致经纱与综丝间摩擦加剧,断头增加。综丝最大密度选择见表1-16。
表1-16 综丝最大密度

表1-7工序项目4设计中,织物为平纹组织,总经根数6488根,穿筘幅153cm,纱线为14.6tex低特纱,设所需综页数为N,则:

因而:

取4页。
2.停经片的(穿)插法 传统织机,如GA 747织机,停经片是闭口式,穿停经片与穿综同步进行(图1-33),而现代织机采用先穿综,再在织机上插停经片的方法。普通织物的停经片可以采用顺穿法,但对于高密纯棉织物,可能由于浆纱被覆不良,产生停经片花衣积聚,织造时断经不关车。因此,可以采用山形穿法,即停经片穿法为1、2、3、4、5、6、5、4、3、2、1的形式,使棉短绒和花衣容易被抖落。

图1-33 穿综工序

穿综

剑杆织造
剑杆织机工艺参数如下。
1.开口(综平)时间
(1)较早开口:非分离筘座织机,如GA 747织机,开口时间为285°~295°;现代分离筘座织机,如THEMA 11织机,开口时间为300°~305°;低特高密府绸织物采用较早开口工艺。
①开口时间早,为引纬提供了较大的空间,打纬时开口高度大,经纱张力大,有利于开清梭口,对于本设计的府绸织物,因经密大、经纱为涤棉经纱、毛羽较长,早开口有利于减少经纱之间的粘连,从而减少“跳花、跳纱、星跳”疵点,也利于织造高纬密织物时打紧纬纱。
②开口时间过早,钢筘打纬时经纱拉伸过度,加上钢筘对经纱的摩擦作用,对低线密度经纱织物,容易产生断头。
③对剑杆织机而言,开口早的同时,梭口闭合时间也早,加剧了剑头退出梭口对上层经纱的挤压摩擦(一般要求:进剑挤压度≤25%,出剑挤压度≤60%),造成布边处上层经纱断头和产生“三跳、纬缩”疵点。
(2)中开口时间:开口时间在320°~325°。
斜纹织物采用较晚开口时间,有利于弱化打纬时上下层经纱张力差异,斜纹线清晰。
(3)晚开口时间:开口时间在330°~340°。
缎纹、小提花、大提花织物采用较晚的开口时间,这是由于这类织物组织循环内交织点较少,每个组织循环内,因打纬导致钢筘对经纱的摩擦作用不大,同时此类织物较多采用低特经纱,较晚的开口时间有利于减少经纱断头率。
一般密度织物晚开口时间为320°,厚型织物晚开口时间为325°,薄型织物晚开口时间为330°~335°。
2.进剑时间
(1)进剑和退剑时间的选择,应减少剑头进出梭口时经纱对剑头产生的挤压度,从而减少边部经纱断头。
(2)有利于提高进剑时送纬剑衔住下降到低点的选纬指中的纬纱的可靠性。
(3)有利于提供足够的引纬时间,有利于增加引纬时剑头对涤棉纱的握持力。
(4)一般接纬剑进入时刻早于送纬剑。
注:GA 747剑杆织机剑头交接、THEMA11剑杆织机接纬剑退出梭口分别如图1-34和图1-35所示。

图1-34 送纬剑和接纬剑交接

图1-35 接纬剑退出梭口
3.后梁高度 调节后梁高度,实际上就是调节经位置线(图1-36)上后梁D1点的高低位置。

图1-36 经位置线
经位置线为胸梁D、织口A、综平时综眼B、停经架导杆C、后梁D1点之间的连线。
经平线a为过胸梁D顶点的水平线。经直线b为织口A到综平时综眼B连线的延长线。
(1)表1-7工序项目5设计为低特高密织物,采用较高后梁工艺,即后梁D在经直线上方,形成上下层经纱张力不同的不等张力梭口,即下层经纱张力大,上层经纱张力小。后梁位置越高,上下层经纱张力差越大。下层经纱张力大,有利于引纬和打紧纬纱;上层张力小,相邻经纱可以相互靠拢,有利于消除高密织物织造时因筘齿厚度而产生的“筘痕”现象。高后梁有利于打纬时纬纱沿经纱的运动,形成紧密织物,也有利于减少打纬时断纬的产生。
但后梁位置过高,下层张力过高,会导致经纱断头增加,同时上层经纱张力过小,导致开口不清,产生“跳花、跳纱、星跳”和“纬缩”疵点。因该设计中织物采用低特经纱,因而后梁高度不能过高。
(2)对于经面斜纹织物,如2/1、3/1等,采用较低的后梁,使得后梁位置在上方接近经直线,上下层经纱张力接近相等,有利于斜纹线“匀、深、直”。
(3)对于经面缎纹织物和小花纹等织物,后梁位置在经直线上,形成上下层经纱张力相等的等张力梭口,有利于花纹匀整。
(4)纬面斜纹,如1/2、1/3、小花纹组织及纬面缎纹为基础的大提花织物,后梁位置低于经直线,形成上层张力大、下层张力小的不等张力梭口,有利于突出纬面花纹效果。
4.停经架高度和前后位置 停经架的位置即停经架导杆C的位置(图1-36、图1-37)除了影响经位置线以外,直接决定了织造中后区梭口L2(图1-36)的清晰情况。涤棉纱毛羽较多、较长,如织物经密较高,经纱在开口时容易彼此粘连,造成开口不清。停经架位置高、位置靠前,后梭口角度β大,后区长度L2短,使得后区经纱在开口时有较大的分纱能力,辅以较大的上机张力,有助于减少涤棉经纱之间的毛羽粘连和分开已粘连的经纱。但后区梭口长度的减小,在一定程度上增加了经纱开口时的伸长率,由于无梭织机梭口高度小,经纱伸长率的增加很小,且涤棉纱弹性较纯棉纱好,断裂伸长率较高,因而不会恶化经纱的工作条件。
5.上机张力 表1-7工序项目3设计为低特高密涤棉织物,涤棉经纱毛羽较多、较长,经密较大,经纱容易彼此粘连,较高的上机张力有利于织造时开清梭口,减少“三跳、纬缩”织疵,同时织物的纬密大,较大的上机张力有助于避免织入织口的纬纱反拨,从而有利于打紧纬纱。
该产品经纱为低特纱,强力低,上机张力过大易产生断头,故上机张力不宜过高。
对于GA747剑杆织机,上机张力的调整是张力重锤通过杠杆原理作用于织机后梁,通过调整重锤重量和力臂长度,对绕过后梁的经纱施加张力。部分新型剑杆织机是通过调整张力弹簧作用点的孔位(图1-38),改变弹簧拉伸量以改变弹力,作用于后梁上,对绕过后梁的经纱施加张力。

图1-37 停经架高度和前后位置调整

图1-38 上机张力调节
喷气织机工艺参数论述见表1-7工序项目6说明,补充说明如下。
1.喷气压力设定
(1)喷气压力设定的意义。
①喷气压力低,气流对纬纱的摩擦牵引力不足,纬纱到达对侧梭口延迟滞后。
②喷气压力不足,纬纱头端飞行无力、飘飞、无法完全伸直,甚至产生扭结,形成布面纬缩疵点,尤其是对弹性较好的涤棉纱和弹力纱产生的疵点更严重。
③喷气压力过大,对于低线密度纬纱,容易因牵引力过大而产生断纬,尤其是在磁针落下,末组喷嘴尚未关闭的情况下,因末组喷气压力又高于前几组,更易断纬。
④喷气压力过大,能耗增加。
(2)喷气气压设定的原则。
①织物幅宽大,气压大些。
②织机速度高、纬纱飞行时间短,气压要大。
③辅喷压力在满足正常引纬的前提下,尽量调低气压,节约用气,辅喷压力略大于主喷压力,因纬纱长度增加,末端辅喷压力要大于前几组辅喷压力。
④设定的总飞行角大,气压可以小些,即采用低压大流量方式引纬。
⑤纬纱线密度高,引纬所需牵引力增大,因而气压增大。
⑥纬纱采用化纤长丝,因其表面较为光滑、气流对纬纱的摩擦牵引作用弱,喷气压力要适当增加,即采用高压小流量方式引纬。
⑦弹力纬纱引纬时,主喷和辅喷的气压都要适当增加。
⑧剪切喷气压以伸直纬纱为准。
(3)喷气压力设定的范围。
①普通纯棉织物:主喷压力为0.25~0.28MPa;辅喷压力为0.3~0.35MPa;
②宽幅纯棉家纺面料、弹性织物、化纤长丝织物:主喷压力为0.30~0.35MPa;辅喷压力为0.35~0.39MPa。
注:主、辅喷嘴如图1-39所示,主、辅喷嘴喷气时间和终端界面如图1-40所示,压力调节旋钮如图1-41所示。

喷气织造

图1-39 喷气织机主、辅喷嘴

图1-40 主、辅喷嘴喷气时间图示和终端界面

图1-41 主、辅喷气压力调节
2.上机张力设定 表1-7工序项目6产品是低特高密涤棉织物,经纱毛羽长、经密大,且喷气织机靠气流牵引纬纱通过梭口,没有载纬器,因而梭口高度小,梭口不易开清。织物的纬密较大,纬纱不易打紧,因此,应采用较大的上机张力。但线密度低,过大的上机张力容易引起经纱断头。

式中,K为强力利用系数,中特、高特织物K=1.15~1.2;低特高密织物K=1.05~1.1;一般密度普通织物K=1;低特稀薄织物K=0.85~0.95。该产品K选1.1,则:
