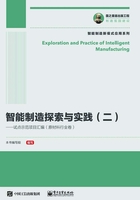
03 氧化铝智能工厂试点示范——山西复晟铝业有限公司
一、项目实施背景与状况
(一)项目实施背景
山西复晟铝业有限公司(以下简称“复晟”)是锦江集团最年轻的氧化铝企业,2013年开始筹建,2014年10月建成投产。在设计规划及装备选型招标过程中,复晟引入了多项行业首创的新技术。同时,为管控信息化的打造实施了以下项目。
(1)统一DCS软件版本,便于后续的开发延伸。
(2)以通信光缆代替硬接线,采集数据链多,施工作业快捷。
(3)增设电动机保护器,采集非变频电气运行数据。
(4)用DCS控制代替PLC控制,数据采集更健全,同时减少柜面投资(磨机系统)。
(5)取消机械式计量仪表,全部采用数字化计量仪表。
(6)流程测计量设备(如温度、压力、流量、液位等),需要的位置一次性配齐。
(7)直接投资建设无人值守地磅系统及客商平台。
(8)采用自动化和数字化程度最高的粉煤炉制煤气系统。
(9)全公司的通信接口统一要求、统一规划,扫清数据之间的互联互通障碍(热电站采用的和利时系统预留的OPC通信接口;南自综保系统预留IEC 104电气规约通信接口等)。
智能化能提升到什么程度,往往取决于企业有什么样的基础。正是因为在建设期间的适当规划和落地,使得复晟的智能工厂提升更具优势和可行性。
(二)项目实施的主要思路和目标
复晟铝业作为行业内第一家智能制造试点示范企业,通过2016年以来的摸索,包括外出培训、考察、多次参加工信部组织的技术、行业交流,复晟全公司上下对氧化铝流程行业智能化提升方向达成了共识。
图3-1是复晟智能工厂总体设计框架,智能工厂的实现至少涵盖4个方面:装备智能化、生产智能化、管理智能化、产品服务智能化。而要实现这4个方面的提升,必须通过硬件/基础支撑层、管理决策层、生产控制层的提升而达到目标。同时,要以装备的数字化为基础(大数据应用及管理),以信息化、互联网为内外沟通的桥梁(“互联网+”,两化融合),在信息安全的前提下实施。

图3-1 复晟智能工厂总体设计框架
二、项目主要实施内容和措施
(一)主要实施内容
1.硬件/基础支撑层
硬件/基础支撑层是智能工厂的基础,以后复晟所有软件系统、控制系统、管理系统都需要依托该基础层的提升程度。推进硬件/基础支撑层建设的步骤如图3-2所示。

图3-2 推进硬件/基础支撑层建设的步骤
智能工厂的基础技术是数据、互联和集成,其作用如下:
(1)数据。数据是开展智能工厂建设的核心,是最基本的要素。因为只有先实现数据化才能实现信息化;实现信息化了,才能形成知识,然后从知识中产生决策,所以说数据是实现智慧工厂的基础。
(2)互联。企业内部需要互联,企业与外部沟通同样需要互联,如各企业之间的数据共享、对标。复晟已经上线了客商平台等,供货方在发货前需提前将信息输入企业的客商平台,驾驶人到达工厂后,只须拿出身份证就能全程自助办理过磅、卸货流程。这些是已经实现了的外部互联,以后还可以增设更多互联。
(3)集成。数据实现互联互通后,下一步就是集成、加工利用这些数据。通过向上引入各种软件平台以共享数据,实现生产、管理的智能化。
(4)提升手段。要提升基础层,必须先实现自动化装备、数字化仪表/传感器、智能化的设备及系统、数字化变配电室的升级和智能化监控水平的提升。
2.管理决策层
复晟的管理决策层分经营管理决策层和生产管理决策层,要提升管理决策层的水平,就需要实现管理层决策的信息化、互联网化、数据化、模型化、无纸化、自动推送化等。推进管理决策层建设的步骤如图3-3所示。
(1)经营管理决策层。集团公司已为下属企业统一规划了NC用友财商库管系统、OA移动办公系统、商务采购招标系统、人力资源(HER)系统,解决了企业在产、供、销、人、财、物及日常审批流程办公的信息化。

图3-3 推进管理决策层建设的步骤
(2)生产管理决策层。复晟根据自身情况,需要在生产管控的决策层面进一步提升,需要提升的有制造执行系统(MES)、生产建模仿真决策系统(SYSCAD)、设备智能点巡检及设备管理诊断系统、配电室智能温控点巡检系统、人事测评互联系统、智能洗车、智能滴灌微喷、一体化破制样系统、自动卸车、自动采样系统、企业一卡通系统、智能停车系统等,主要目的是使生产管理和控制达到自动化、智能化、信息化,从而为生产管控的决策提供帮助。
3.生产控制层
衡量流程型冶金行业智能化程度的高低时,一个非常重要的指标是生产控制层的智能化程度。因为生产控制层直接体现企业智能化水平,大部分的软/硬件的基础投入,都是为了最终体现在生产控制中,劳动强度的降低、产品质量/指标的把控、人均产值的提升、管理效率的提升,也都是为了体现生产控制层的智能程度。流程型制造业与加工制造业不同,流程型制造业需要用智能模型控制代替人工操作控制,好比制造业用机器人代替人、用人工智能代替人。图3-4所示为推进生产控制层建设的步骤。

图3-4 推进生产控制层建设的步骤
生产控制层在有数据输入的情况下,通过数学模型和仿真系统的导入,实际上是可以实现智能控制的。通过数学模型,能够提前预判未来趋势;通过仿真系统,能够实时控制多个相关变量参数,将目标控制在设定的范围。
(二)采取的主要措施
本项目采取的主要措施如下:
1)实施路径
在实施过程中,在整个工作安排上,根据不同专业,分4个路径去实施,分别如下:
(1)现有工艺装备的自动化升级。
(2)引入智能装备及系统。
(3)提升管控信息化水平。
(4)实现智能动态控制。
2)实施方式
(1)划定“红线”。智能工厂的建设没有统一的执行标准,行业不同、企业基础现状不同,实施的方式和步骤也一定不同,但方向和目标一定是一致的。通过装备水平和信息技术水平的提升,以代替人的脑力和体力,这是智能工厂的意义所在。复晟以这个杠杆作为打造智能工厂的“红线”,方向就不会走偏。
(2)项目落地前的决策。在落地前,每个拟实施的项目还需要有一个判断和抉择的过程,包括以下4个方面:
①投资情况。
②实际的可操作性和可行性。
③分几个步骤实施。
④企业受益点。
(3)管理方式的跟进。新技术、新装备的引入,一定需要新的管理模式,复晟一直号召“不能一边用着21世纪的装备,一边还沿用19世纪的管理模式”。
(4)培育包容的创新文化氛围。智能工厂的打造实际上是不断创新的过程,涉及企业的方方面面,是一项全局性的工作,不能仅靠个人。复晟已将智能工厂的创建、企业的创新作为企业文化来塑造,并且对待创新已经形成了包容的文化氛围,创新行为不能有束缚,也不可能保证所有项目都能正中靶心,一定会有失败或者暂停的项目。所有项目当中不乏众多经过调研、考察、评估而暂停的,但是整个创新过程,企业一定是受益的。企业对每个项目都成立项目阶段小组,目标任务完成后都会对小组成员进行嘉奖。同时,组织不同岗位和不同职位的人员外出培训、参观、交流也成为常态。“包容、不束缚、肯定、学习进步”的创新文化氛围,贯穿整个智能工厂建设过程。
三、实施成效
复晟氧化铝智能工厂项目实施后,在工艺装备自动化、智能装备及系统、管控信息化提升、智能动态控制等方面取得了明显的效果。
(一)管控信息化
1.自主开发制造执行系统(MES)
为满足生产管理需求,复晟信息部自主开发了一套制造执行系统(MES)如图3-5所示。该系统包括质量管理模块、技术管理模块、生产管理模块、能源管理模块、绩效管理模块、实时数据模块、设备管理模块、生产建模八大模块,大大提高了生产管控一体化水平。

图3-5 自主开发的制造执行系统(MES)
2.开发第三方App
为了配合MES的功能性扩展需求,完善原始系统的不足,满足用户的个性化需求,开发了第三方App,如图3-6所示。该App对影响生产的几类指标进行归纳整理,通过MES提供的既定接口和已封装完善的数据框架,将MES关注度较高的各类指标详尽展示。同时将内网与外网打通,让用户随时随地通过此款App查看各项指标的详细状况,收到实时预警信息。
3.上线客商物联平台
虽然目前地磅房已实现自动过磅,但是货车驾驶人还需排队领取计量卡与质检卡,在此环节浪费了大量时间。地磅房客商物联平台(见图3-7)的上线,减少了过磅过程中人工参与,真正实现无人值守。地磅房客商物联平台的应用,提高了地磅房的自动化水平。

图3-6 第三方App

图3-7 地磅房客商物联平台
(二)智能装备系统
1.生产设备智能点巡检管理系统
生产设备智能点巡检管理系统如图3-8所示。目前该系统已经实现全厂覆盖,涵盖设备498台、3937项巡检项,巡检手段囊括测振、测温、观察、抄表、预设状况等,建立A类设备专家预诊断、故障系统,可自动、快速地判断设备故障的可能原因,更加有利于指导设备检修。上位机增加了微信App推送功能,可将异常信息等推送至指定的管理群。

图3-8 生产设备智能点巡检管理系统
2.铝矿石全自动破制样系统
在项目实施前,质检站的破制样过程全部在监控下完成,员工劳动强度和心理压力都大。同时,作业车间也有较大粉尘,影响员工的健康。铝矿石全自动破制样系统(见图3-9)投入使用后,整个破制样过程无须人工参与,原来矿石破制工序至少需要4人,现在只需要2人,员工劳动强度降低,工作环境大大改善。

图3-9 铝矿石全自动破制样系统
3.配电室智能温控点巡检管理系统
为加强配电室的安全管理、降低员工的劳动强度,复晟引进了配电室智能温控点巡检管理系统,如图3-10所示。该系统采用无线信号接入,实现上位机超温警告及一键查看、手动复位、温度查询、报警、设置、手机群发短信报警等管理功能,替代人工点巡检、测温及测电流,及时发现隐患。

图3-10 配电室智能温控点巡检管理系统
4.在线自动煤取样系统
项目实施前,进行煤取样时一般由人工直接从皮带机上取样,这种人工操作和取样方式对化验结果有较大的影响。对此,复晟引进了在线自动煤取样系统,如图3-11所示。该系统具备自动采样、破碎、缩分及弃样返回等功能,大大降低了员工的劳动强度,减少了人工采样带来的化验结果误差。

图3-11 在线自动煤取样系统
(三)现有工艺、装备的自动化(数字化)升级
1.焙烧刮板取料机的远程控制
为解决焙烧刮板取料机无法远程控制的问题,公司信息部利用现有的分散控制系统(DCS)接入无线信号,加装模块及软件,使其具有组态画面、报警及趋势显示功能。可顺利完成取料机主画面的远程操作,自定取料速度,提升DCS智能控制水平。焙烧刮板取料机的远程控制如图3-12所示。

图3-12 焙烧刮板取料机的远程控制
2.高压真空泵的远程控制
为解决高压真空泵无法远程监控的问题,公司信息部利用现有DCS接入无线信号,加装模块和软件,显示组态画面、报警及趋势,监控主画面的运行及电流信号,查看历史数据。同时方便后续运行时间及用电量编程的汇总,进一步提升了DCS智能控制水平。高压真空泵的远程控制如图3-13所示。

图3-13 高压真空泵的远程控制
3.圆锥破碎机的远程监控
为进一步监控管控中心设备运行状况,公司信息部对2台圆锥破碎机进行了技术改造,实现远程监控。主控室可以及时查看和掌握现场设备运行状况和参数状态,手动或自动调整间隙大小,保证破碎物料满足生产工艺要求。圆锥破碎机的远程监控如图3-14所示。

图3-14 圆锥破碎机的远程监控
4.溶出套管换热的监控
为解决生产工艺人员无法调整溶出套管换热系数的难题,公司信息部与技术部协作,结合DCS情况,对溶出车间自动计算换热系数。根据现场实际反馈量,利用软件,按技术部要求对各个变量进行运算,自动计算出各级的换热系数,并且实时显示数据,如图3-15所示。

图3-15 溶出套管换热的监控
(四)智能动态控制
1.指标自动连锁控制
指标自动连锁控制(见图3-16)包括溶出液的Rp值的自动连锁控制和蒸发车间的第四级闪蒸器放出的液体浓度值自动连锁控制。在线仪表的投用可在线了解指标的变化,降低指标波动范围,使生产控制精细化,提高运行效益。

图3-16 指标自动连锁控制
2.锅炉燃煤APC自动控制系统
锅炉燃煤APC自动控制系统(见图3-17)是公司正式投入使用的第一套自动控制系统,该系统的投用提升了锅炉自动化控制率,确保了锅炉安全稳定运行,并且提高了锅炉热利用率。

图3-17 锅炉燃煤APC自动控制系统
四、实施经验
复晟氧化铝智能工厂试点示范项目的实施,取得了良好成绩。虽然在实施过程中遇到了许多困难,但是在攻坚克难的过程中,积累了许多成功经验。
(1)复晟自主开发的项目较多,对此,公司成立了软件开发小组。2016年,软件开发小组为公司开发了制造执行系统(MES)及移动生产管控系统手机App。这些系统的投入对公司管理效率的提升及管控精细化起到了促进作用,因此,在接下来的智能工厂试点示范项目实施过程中,软件的自主开发仍是主要工作。
(2)2016年,在智能工厂试点示范项目实施过程中,由于很多子项目是首次开发的,没有成熟的经验和供应商可供选择。通过公司的实践与摸索,该项目有了很好的示范和推广作用。
(3)复晟智能工厂的打造不是依靠一两个人的想法,而是发动全体员工共同参与,充分尊重员工的想法。复晟智能工厂的打造不仅拓宽了员工知识面,而且大大开阔了员工眼界。
(刘凯、沈亚 供稿)