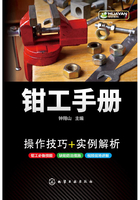
第3章 锯切
3.1 锯切基本技能
用手锯对工件进行切断和切槽的加工操作称为锯切。锯切主要应用有:①锯断各种原材料或半成品,见图3-1(a);②锯掉工件上的多余部分,见图3-1(b);
③在工件上锯槽等,见图3-1(c)。

图3-1 锯切的应用
3.1.1 锯切工具
钳工的锯切加工通常由手锯来完成,手锯由锯弓和锯条组成。
(1)锯弓
锯弓是用来安装和张紧锯条的,分可调式和固定式两种,其结构如图3-2所示。

图3-2 锯弓的形式
(2)锯条
锯条一般是由T10、T10A碳素工具钢制成的,经过热处理,其硬度不小于62HRC。锯条的基本结构是由锯齿(工作部分)、条身和销孔等构成的,如图3-3所示。

图3-3 锯条结构
1, 4—销孔;2—锯齿;3—条身
1)锯条规格
锯条规格包含两种情况,一种是指长度规格,另一种是指锯齿规格。
① 长度规格。长度规格是以两端安装孔之间的中心距长度来表示的,其规格有200mm、250mm和300mm三种,钳工常用的是300mm。
② 锯齿规格。锯齿规格分为粗齿、中齿、细齿三种情况,有两种表示方法:一种是以每25mm长度内的齿数来表示,如粗齿为14~18、中齿为22~24、细齿为32;另一种是以齿距来表示,如粗齿为1.8mm、中齿为1.2mm、细齿为1.1mm。
2)锯齿形状及切削角度
锯齿形状及切削角度如图3-4所示。

图3-4 锯齿形状及切削角度
① 后角α0。后刀面与已加工表面之间的夹角称为后角。后角一般为35°~40°,后角越大,摩擦力就越小。
② 楔角β0。后刀面与前刀面之间的夹角称为楔角。楔角一般为45°~50°,楔角越大,锯齿强度就越大。
③ 前角γ0。前刀面与待加工表面之间的夹角称为前角。前角一般为0°~10°,前角越大,锯削越锋利。
④ 齿距B。两齿尖之间的距离称为齿距。
3)锯路
为保障锯齿自由切削,在制造锯条时,锯齿按一定要求左右错开所排成的形状称为锯路。锯路分为交叉形[见图3-5(a)]和波浪形[见图3-5(b)]两种。锯条条身的厚度一般为0.6~0.7mm,锯路的宽度一般为0.9~1mm,如图3-5(c)所示。这样在锯削时,锯条既不会被卡住,又能减小锯削过程中的摩擦阻力;同时,锯条也不致因为摩擦过热而加快磨损,从而延长了锯条使用寿命。

图3-5 锯路
4)锯条的选用
粗齿锯条一般锯削较软的材料,如铜件、铝件、铸件以及比较软的(低碳钢)钢件等;细齿锯条一般锯削较硬和较薄的材料,如(中碳钢、高碳钢)钢件、薄壁管件;中齿锯条锯削的材料范围较广。表3-1给出了锯齿的粗细规格及应用。
表3-1 锯齿的粗细规格及应用

3.1.2 锯条的安装与锯切的姿势
锯削操作加工的质量及锯条的安装及锯切姿势的正确性关系极大,主要应注意以下几方面。
(1)锯条安装方法
锯条安装时,右手握弓柄,左手首先适当调松后锯钮的蝶形螺母,再持锯条,注意观察齿尖方向(齿尖应向前),先挂后锯钮销,后挂前锯钮销,然后尽量调紧锯条,如图3-6所示。锯条安装既不能调得太紧也不能调得太松,否则锯切时,容易造成锯条折断或使锯缝歪斜。此外,锯条安装后应检查锯条是否歪斜和扭曲,如锯缝超过锯弓高度时,应将锯条与锯弓成90°安装。
(2)锯削姿势
锯削的姿势正确与否直接影响到锯削操作的质量,锯削操作姿势主要应做好以下方面的工作。
① 锯弓的握法。锯弓的握法正确与否对锯削质量有很大的影响,正确的握法应是左手轻扶锯弓前端,右手握住锯柄,如图3-7所示。

② 站立位置。操作者应面对台虎钳,站在台虎钳中心线一侧,左脚与台虎钳中心线成30°,右脚与台虎钳中心线成75°,如图3-8所示。这种站立方式可使站立者稳定,便于锯削。

图3-8 锯削站立位置
③ 锯削姿势。锯削时的站立位置和身体摆动姿势如图3-9所示。锯削时手锯稍作上下摆动,当手锯推进时,身体略向前倾,双手随着压向手锯的同时,左手稍微上翘,右手稍作下压。当手锯回程时,右手稍微上抬,左手自然回收以减少切削阻力,提高工作效率,并且操作自然,双手不易疲劳。但锯削对锯缝底面要求平直和薄壁工作时,则双手不用摆动,只能做直线运动。锯削时应尽量利用锯条的有效长度。锯削软材料和非铁金属材料时,推动频率为每分钟往复50~60次,锯削普通钢材时,推拉频率为每分钟往复30~40次。

图3-9 锯削姿势
3.1.3 锯切基本操作技术
锯削操作时,首先应做好工件的装夹,做好锯削前的起锯,然后根据所锯削工件的形状选用合理的操作方法。
(1)工件的装夹
工件一般应夹在台虎钳的左面,以便操作;伸出钳口不应过长,应使锯缝离开钳口侧面20mm左右,防止工件在锯削时产生振动;锯缝线要与钳口侧面保持平行,便于控制锯缝不偏离划线线条;夹紧要牢靠,还要避免将工件装夹变形或夹坏已加工好的平面。
(2)起锯的方法
在工件的边缘处进行锯缝定位时的锯削称为起锯。起锯分为前起锯、后起锯和后拉起锯三种方法。
① 前起锯。在工件的前端开始起锯,起锯前,用左手拇指或食指的指甲盖抵住锯条的条身进行锯缝定位,然后倾斜15°左右的起锯角度,保证至少有三个锯齿参加切削,以防止卡断锯齿,如图3-10所示。

图3-10 前起锯方法
起锯时,锯削运动的速度控制在25次/min左右,行程控制在150mm左右,压力要小。当锯到槽深3~4mm时,起锯完成,左手拇指或食指即可离开锯条,扶在前弓架端部进行全程锯削。
② 后起锯。在工件的后端开始起锯,起锯前,用左手拇指或食指的指甲盖抵住锯条的条身进行锯缝定位,然后倾斜15°左右的起锯角度,如图3-11所示。起锯时,锯削运动的速度控制在25次/min左右,行程控制在150mm左右,压力要小。当锯到槽深3~4mm时,左手拇指或食指即可离开锯条,扶在前弓架端部进行全程锯削。

图3-11 后起锯方法
③ 后拉起锯。在工件的后端开始起锯,起锯前,不用左手拇指或食指的指甲盖抵住锯条的条身进行锯缝定位,而是直接将锯条的后端放在锯缝位置,倾斜15°左右的起锯角度,如图3-12所示。起锯时,是将锯条自前向后拉动锯削,一次锯削行程后,再抬起锯条并将锯条的后端放在锯缝位置,再自前向后拉动锯削。后拉起锯的特点,一是不挂齿,二是振动很小、定位稳定。后拉起锯的速度控制在20次/min左右,行程控制在200mm左右,压力要稍大一点,当锯到槽深3~4mm时,起锯完成,进入全程锯削。

图3-12 后拉起锯方法
(3)锯切的操作要领
① 中途锯削。当起锯到槽深3~4mm时,起锯即告完成,这时就进入中途锯削阶段。中途锯削时,锯齿应尽量全部参加切削行程。为提高锯削效率,在每次锯削行程中,锯弓可作一个小幅度的、自然的上下摆动,即前1/2行程时,前弓架低,后1/2行程时,后弓架低。要注意的是,上下摆动的幅度不宜过大,因为摆动幅度过大,锯缝容易发生歪斜。
② 锯削速度。全程锯削时的锯削速度控制在20~40次/min左右,锯软材料可以快些,锯硬材料应慢些,且锯削行程不应小于锯条全长的三分之二。锯切速度过快时,锯条发热严重,容易磨损,必要时可加水、乳化液或机油进行冷却润滑,以减轻锯条的发热磨损。
③ 推力和压力。锯削运动时,推力和压力由右手控制,左手主要配合右手扶正锯弓,压力不要过大。手锯推进时为切削行程,应该施加压力,返回行程不切削,则不施加压力,自然拉回即可。
④ 收锯。收锯形式有两种:一种是对将要锯断的工件而言,当接近边缘时,应逐渐降低锯削速度、减轻推力和压力,锯条倾斜一定角度并直线往返锯削直至锯断;另一种是对将要锯至一定深度的工件而言,当锯至接近深度位置时,逐渐降低锯削速度、减轻推力和压力,水平直线往复锯削至深度要求位置。
3.1.4 锯切操作注意事项
锯切操作时,操作人员除需掌握基本的操作技术外,为保证操作的质量,还应具备现场操作缺陷的处理技能,同时保证操作的安全性。
(1)锯缝歪斜的防止和纠正方法
锯条安装夹紧后,其侧平面一般并不是和弓架的侧平面处于同一平面或构成平行的状态,这时可利用一些工具进行适当矫正。但条身与弓架的侧平面仍然有一定的倾斜角度α,如图3-13(a)所示。如果以弓架的侧平面为基准对工件进行锯削,锯缝就容易发生歪斜,如图3-13(b)所示。
因此,在锯削过程中,可从以下方面防止锯缝的歪斜:一是弓架的握持与运动要以条身侧平面为基准,条身应与加工线平行或重合,如图3-13(c)所示;二是在锯削中应不断观察并及时调整,这样才能有效地防止锯缝歪斜。
在锯削加工中,锯缝如果发生较明显歪斜时,如图3-13(d)所示,可利用锯路的特点采用“悬空锯”的方法进行纠正。其操作方法是,先将锯条尽量调紧绷直,将条身悬于锯缝歪斜的弯曲部位稍上位置,如图3-13(e)所示,左手拇指与食指、中指相对地捏住条身前1/3处,并适度用力扭转条身向弯曲点一侧自上而下地进行修正锯削。此时,锯削行程不宜过长,一般控制在80mm左右,当修正的锯缝与加工线平行或重合时,即可恢复正常锯削,如图3-13(f)所示。

图3-13 锯缝歪斜的防止和纠正方法
(2)锯切操作注意事项
① 握持锯弓时,注意手指不要伸到弓架内侧,特别是左手不要抓握弓架,防止手被碰伤。
② 在台虎钳上装夹工件时,一般情况下,工件的锯削位置多在台虎钳的左侧,这样比较方便和顺手。工件的锯缝位置应离钳口侧面20mm左右(如图3-14所示),如果锯缝位置离钳口过近,握持手柄的手在锯削时容易碰到台虎钳而受伤;如果锯缝位置离钳口过远,则在锯削时容易产生振动而导致断齿;锯削加工线应与钳口侧面保持平行。

图3-14 工件的装夹
③ 锯削时用力要适当,摆动幅度不要过大,要控制好速度(节奏),不可突然加速或用力过猛,以防锯条折断伤手以及手碰到台虎钳受伤。
④ 当工件将要锯断时,应减小锯削压力,避免因工件突然断开时,握持手柄的手仍然在向前用力而碰到台虎钳受伤。
⑤ 当工件将要断开时,应该用左手握住工件将要断开的部分,同时应减小锯削压力和降低锯削速度,避免工件掉下伤脚。