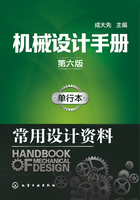
3.3 有凸缘圆筒形件的拉深
(1)有凸缘圆筒形件毛坯直径的计算和修边余量的确定
有凸缘圆筒形件毛坯直径D的计算按式(1-3-4):
(1-3-4)

图1-3-3 有凸缘圆筒形件
表1-3-47 有凸缘圆筒形件的修边余量Δdf的确定

(2)首次拉深的最大相对高度和极限拉深系数
有凸缘圆筒形件首次拉深的最大相对高度、极限拉深系数见表1-3-48。对于以后各次拉深,可相应地选取表1-3-45中的[m2]、[m3]……[mi]。
表1-3-48 有凸缘圆筒形件首次拉深的最大相对高度[h1/d1],首次拉深的极限拉深系数[m1]

注:1.表中系数适用于08、10号钢。对于其他材料,可根据其成形性能的优劣对表中数值作适当修正。
2.最大相对高度部分较小值对应于工件圆角半径较小的情况,即rp、rd=(4~8)t;较大值对应于工件圆角半径较大的情况,即rp、rd=(10~20)t。
(3)多次拉深的设计原则
有凸缘圆筒形件的多次拉深可按如下原则进行设计:
①对于窄凸缘圆筒形件(df/d=11~14),前几次拉深中不留凸缘或只留凸缘和圆角部分,而在以后的拉深中形成锥形凸缘,并于整形工序中将凸缘压平。
②对于宽凸缘圆筒形件(df/d>14),应在首次拉深中形成工件要求的凸缘直径,而在以后的拉深中凸缘直径保持不变。
a.当毛坯相对厚度较大时,应在首次拉深中得到凸缘与底部圆角半径较大的中间毛坯,而在以后的拉深中制件高度基本保持不变,仅减小圆筒直径和圆角半径。
b.当毛坯相对厚度较小并且首次拉深圆角半径较大的中间毛坯具有起皱危险时,应按正常圆角半径大小进行首次拉深设计,而在以后的拉深中制件圆角半径基本保持不变,仅以减小圆筒直径来增大制件高度。
③为了避免凸缘直径在以后的拉深中发生收缩变形,宽凸缘圆筒形件首次拉深时拉入凹模的毛坯面积(凸缘圆角以内的部分,包括凸缘圆角)应加大3%~10%。多余材料在以后的拉深中,逐次将15%~3%的部分挤回到凸缘位置,使凸缘增厚。
④当工件的凸缘与底部圆角半径过小时,可先以适当的圆角半径拉深成形,然后再整形至工件要求的圆角尺寸。
(4)拉深次数及各次拉深变形尺寸的确定
确定有凸缘圆筒形件拉深次数及各次拉深变形尺寸的步骤和方法如下:
①按表1-3-47确定修边余量Δdf。
②按式(1-3-4)计算毛坯直径D。
③计算t/D×100和df/d,从表1-3-48中查得首次拉深的最大相对高度[h1/d1],然后与工件的相对高度h/d进行比较,判断能否一次拉深成形。
④如需多次拉深,则先用逼近法确定首次拉深的圆筒直径d1和极限拉深系数[m1],再从表1-3-45中查得以后各次拉深的极限拉深系数。依次计算各次拉深的极限拉深直径,一直计算到小于或等于工件要求的尺寸,从而得到工件所需的拉深次数。
⑤拉深次数确定以后,为使各次拉深变形程度分配更为合理,应调整各次拉深系数,并使之满足:d=m1m2…miD。
⑥根据上面(3)中③原则,重新计算毛坯直径D。
⑦根据调整后的毛坯直径和拉深系数计算各次拉深直径。
⑧确定各工序制件的凸缘与底部圆角半径。
⑨按下式计算各工序制件的高度。
(1-3-5)
式中,符号下标i=1、2、3…,表示第i次拉深。
⑩校核首次拉深的制件相对高度。如果首次拉深的h1/d1>[h1/d1],则应重新调整各次拉深系数。